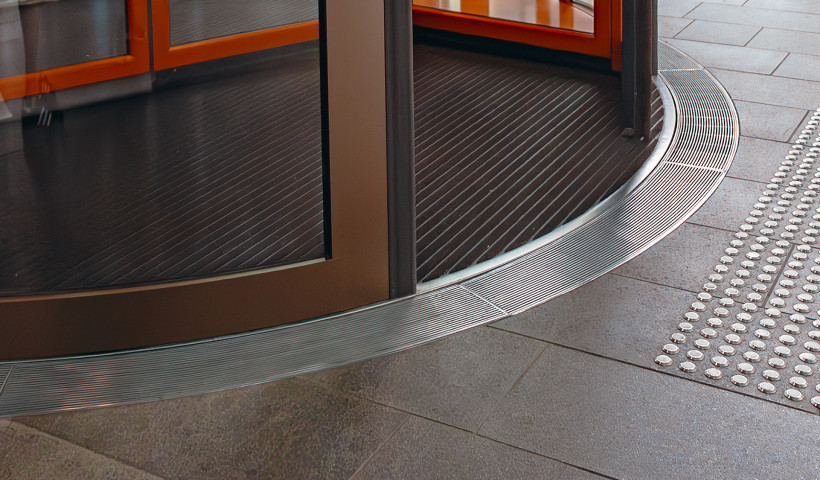
Support local manufacturing
Local manufacturers have the knowledge and experience to put forward solutions that fit with regulatory requirements. No offers of “this will work” or “we can get this in for you.” Locally made is made for local.
Ian Jackson, the owner of Allproof industries got his plumbing certificate in 1958, his father before him in 1926. Ian was heavily involved in the adoption of the AS/NZS3500.2 plumbing standard into New Zealand and to this day directs the company to be a solution based, compliant manufacturing company.
Reduction of embedded carbon in products is a high focus for the next generation of the family, and can be broken down into a few focus points.
Transport
Offshore manufacture will give the supplier no option other than reliance on a path to site of thousands of kilometres. Think about it, from the plant to the local depot, the local depot to the port and then the long sea freight journey to the NZ shore. All of this out of the manufacturer's control. Allproof’s longest path to site in NZ is approx. 1600KM. If you look at an application such as a commercial kitchen floor waste system, the locally made option will allow for both a fast turnaround standardised option, as well as the ability to select a custom fabricated solution that has nationwide site support to ensure the selected product is detailed, drawn and supplied to site in a timely manner and to meet the site requirements.
The manufacturing process
Allproof aren’t putting energy into offsetting carbon by buying credits, they are fixing their home first. Constant improvement of internal systems is externally audited in order to achieve best environmental practice, proving an ongoing commitment. Installation of a 1000Kw/Hr solar plant provides onsite renewable energy to power the production plant, along with forklifts, staff and delivery vehicles. This installation reduces the amount of carbon released into the atmosphere of more than 50 tonnes per annum. Waste material from the manufacturing process is reground to then be used again in the moulding process, some of the products are even made from 100% Auckland kerb side recycled material. Rain water harvesting, waste separation for recycling and fully biodegradable pallet wrap and packaging tape adds to the full picture of sustainability.
Constant improvement of the production process including investment in on site material recycling systems and electricity friendly machinery, carbon reducing solar sourced power, electric and hybrid fleet and rubbish management all contribute to the final outcome you are looking to select.
Product life cycle
The core basis of moulding PVC products make it difficult to achieve a green rating, however, Best Environmental Practice (BEP) certification ensures that the PVC product sent to site has been manufactured to the best possible standard. 50 year life cycle, and the ability of the product to be 100% recycled at this point should be noted. Again, with the mileage this product would do in this full life cycle, it can’t be matched by offshore supply.
You have the option of selecting a level threshold or surface drainage system that provides a reduced carbon footprint, with a selection of locally made, 100% recycled material solutions manufactured using renewable solar energy — it’s as simple as selecting Allproof.