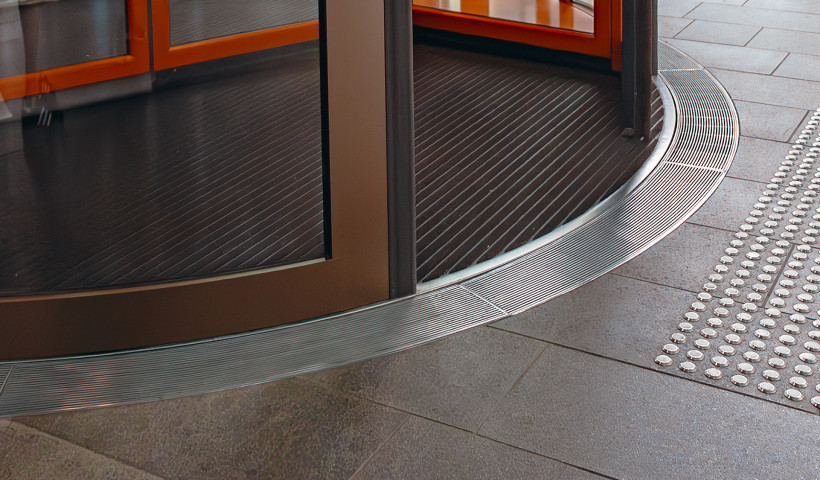
In designing the repurposed B201 building for Auckland University, Jasmax faced challenges around coordinating services into the existing structure..
The new two storey high atrium with a steel/timber hybrid structure spanning 35m had the roof elements visible in a majestic manner. This created a design opportunity for a bespoke solution to the disposal of stormwater from the 1500m² roof. The solution was to slope the whole roof towards the east block and discharge the stormwater through just five custom rainwater sumps into 300mm diameter internal downpipes.
At this point Jasmax designers leaned on the experience and local manufacturing strength of Allproof to help meet the installation’s needs. Several face-to-face meetings and design revisions were worked through to ensure both the membrane above the gutter, and the multiple 300mm diameter PVC outlets and overflows below the gutter worked to performance, installation, and buildability requirements. Due to the necessity of a high-capacity flowrate, the outlets Allproof designed and manufactured incorporated a custom bolted flange solution. The flange was laser cut in-house at Allproof to allow a bolted union on the outlets ensuring that, when fully charged, the connection was secure and durable.
Custom stainless-steel sumps incorporating clamping rings, and removable perforated domes went through a thorough design and review process. Considering the leafy environment, access and maintenance of the outlets became an imperative design feature along with the hydraulic performance and a secure membrane termination.
Two 300mm outlets, one primary and the other overflow, needed to be built into the BIM (Building Information Modelling) model transporting rainwater to a stormwater connection through a limited space. This is where the custom stainless-steel solution came into its own. Depth and angle of outlets were reviewed and incorporated into the product design to remove any clashes with other services or structural elements and resulted in a seamless install.
As overflows need to be sent to atmosphere, this resulted in an unsightly pipe protruding into the pedestrian pathway on the side of the building. The 300mm diameter opening of the pipe created a risk of vermin entry to the overflow system and a visual impact. Again, the design teams from Jasmax and Allproof collaborated to create a bespoke overflow cover that satisfied hydraulic requirements, was secure, and of most importance looked in place on the face of this refurbishment.
Allproof’s Perimeter drain was used as the level threshold solution at the entrance to the atrium and lower level podium providing an accessible entryway. The 316-grade stainless steel wedge wire grate was selected to provide a premium aesthetic while also benefiting from its design features such as heelproof grating and an R11 slip resistance (AS4586). In this area, the glazing selection resulted in the sill of the window protruding beyond the glazing line, below paved level. In order to maintain the required 12mm gap Allproof provided a customised fold from the grating to span this sill and create a detail that satisfied both form and function.
The loading dock entrance is subject to large commercial vehicle access and movement. Therefore, Jasmax selected Allproof’s 200mm clear opening Polymer Concrete channel drain with cast iron grate due to its high-performance characteristics in this environment. The channel drain has excellent catchment and hydraulic performance, to achieve load class E rating in accordance with AS3996, a minimum 200mm concrete surround was detailed for the install. Cast iron is resistant to dynamic wheel loads such as trucks manoeuvering or forklifts turning on them as well as good vibration dampening which helps protect surrounding concrete. Grate lockdowns are imperative in this situation to prevent the small movement of grates knocking against the channel edges under heavy wheel loads.
The final result of B201 is a testament to Jasmax and Allproof working in collaboration to achieve results that meet all design requirements. Focusing on design, integration, performance, and most of all, detail, ensured the project was delivered to specification.