What is productivity?
Productivity is how much you get out from what you put in so is measured as outputs divided by inputs. The more you get out or the less you put in improves productivity.
The graph below shows the construction sector's labour productivity in red compared to other selected industries. As you can see, construction is more productive than it was in 1978, but much less so than other industry sectors. This shows a few example sectors to keep the graph simple, but the overall message is consistent: construction as a sector lags behind most of the economy.
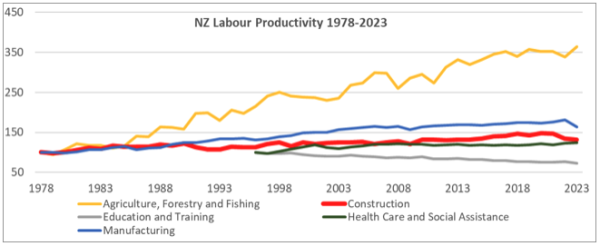
Source: Stats NZ. 1978 = 100
New Zealand’s economic wellbeing is still underpinned by our primary sector. Despite being 'traditional' industries, the willingness of these sectors to invest in and adopt new technologies and processes is impressive. This shows through in their productivity.
The car manufacturing industry has a concept, from Toyota, I think, “mountains made of sand”. The idea being that a lot of small improvements add up to a big one. This approach shows through in the gradual, but constant, increase in manufacturing productivity.
Construction isn’t the only sector that struggles with productivity. Every governmental budget cycle there is a cry for more money for education and healthcare. While technology impacts education, nothing can replace face to face time with teachers; the OECD ideal class size is around 14. In fact, technology probably means that there is more to teach. Healthcare is worse as they are developing new and improved cures that take more time and cost more. So, both need a greater share of the tax dollar.
What does this matter?
If you spend a 1978 dollar in the primary sector now, you’ll get much more value for it than you will from construction. Construction becomes more expensive as other industries produce more with less.
Labour is the single largest cost to residential construction so is the obvious place start looking for efficiencies.
In the below table we calculate labour and materials for different trades. Some labour content been estimated for the purpose of this exercise.
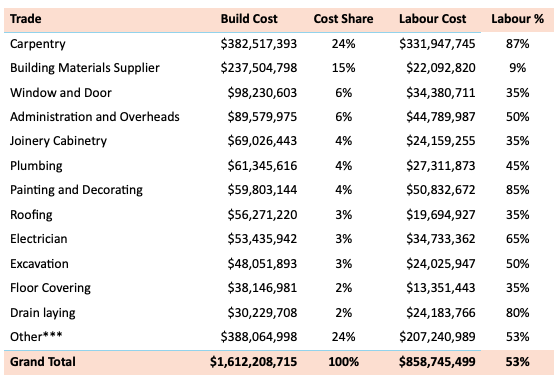
*Includes frame and truss manufacture
**Includes plumbing fixtures
***Other is the 89 trades that account for less than 2% of the total
The labour content is similar across new builds and renovation:
We must improve labour productivity to lower housing costs
To lower the labour cost, we could drop wages (not likely to go down well), or we could change the way we work to get more for return on our efforts. Working longer or harder isn’t the answer, being more effective with our time is.
This means that to reduce the real cost of building houses, we must improve labour productivity. Focusing on the cost of say building materials, at 15% of the total cost, is fiddling at the edges if 50% of the cost is underperforming.
Building a house is very complex and subject to a lot of regulation. The combination of this impacts on productivity and constrains the ability to improve it.
We are a fragmented industry of small businesses
Fragmentation and small size of the companies involved is drag on productivity and our ability to improve it. Larger businesses can invest resources in improving their businesses. For smaller business, dealing with today tends to draw the bulk of their focus. (YourQS is unusual for a small NZ business, we invest heavily in R&D and process improvement as we have a big vision and the belief that we can make a difference.)
The issue of a fragmented industry and housing affordability is not unique to NZ construction.
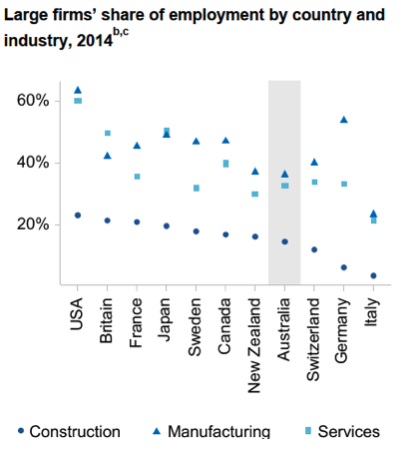
Source Australian Productivity Commission. Housing construction productivity: Can we fix it? Feb 2025
There are no magic bullets
As successive Governments have found, changing the sector is not easy as there is no single answer short-term fix. Allowing the import substitution of plasterboard etc. is not going to make a jot of difference. There isn’t a magic construction system out there that is going to revolutionise building. Instead, we must look to manufacturing for the answer. This doesn’t necessarily mean building houses in factories, but taking on the concept of constant small improvements across the industry.
Some areas to look at:
- Processes: Understand that everything is interlinked as a process and look for inefficiency, waste or redundancy to remove.
- Standardisation: Being a small market, our houses are always going to be relatively bespoke. Standardising not only building components but also data and processes will lead to efficiencies.
- Scheduling: The elapsed time to build a house bears little comparison to the actual labour hours employed. Bringing these closer represents a significant cost reduction opportunity.
- Regulatory: Local and central government rules and policies have a material impact on costs.
- Technology: The construction sector is a low and slow adopter of technology — something that has delivered gains in other sectors.
About Nick Clements
Nick won the inaugural NZIOB 2024 Digital Technology award for his work on 3D estimating in residential construction. He is a Member of the NZIQS and is vice chair of the Auckland committee.
His business, YourQS, specialises in providing cost estimating services to residential builders, architects, and homeowners for both new build and renovation projects. They have completed over 3,200 projects since launching in 2019 working for around 300 builders nationwide.
Nick is the host of the Beyond the Guesstimate podcast where he talks with interesting people ideas on how we can improve as an industry and as businesses within it.