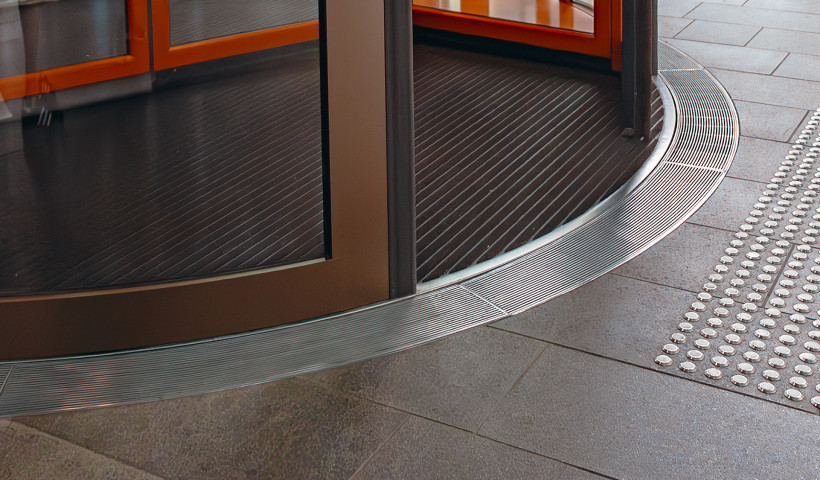
Multi-unit housing places individual tenancies adjacent to each other. Each of these tenancies are required to be their own individual fire cell constructed with fire rated walls, ceilings and floors. Any penetrations into this cell, for an electrical, water or waste pipe, will require a passive fire solution which will activate in the event of a fire and insulate the gap in the fire cell the penetration has created.
When designing the construction of fire cells there are some key points that need consideration for elements that require passive fire protection. For example, plumbing systems that are in the wall or ceiling may need fall over a considerable distance. This could then require pipe work for waste being placed in positions where it may affect how a passive fire protection system is applied whether it be a plasterboard or a concrete substrate.
Wet areas on intertenancy walls will require design around how the fire cell is achieved and how the water or electrical penetrations terminate through the wall faces. A plasterboard fire baffle may need to be built in the wall space where the electrical or plumbing service exits, in between nogs and stud work. The pipe work and wires are then treated in wall by a fire collar where they enter the baffle and before they terminate at the fixture or fitting.
Passive fire protection systems need to be exposed so that the intumescent will activate in a fire situation, some planning may be required for services with limited space where it penetrates a fire cell. This would be seen at waste or soil pipe positions as the pipe work enters the space to service the sanitary fixtures. If a vanity unit or kitchen cabinet is on the wall face, design is required around how the fire collar can activate as the intumescent in the collar cannot be covered/insulated by cabinetry or a finishing flange.
Pipe work or electrical wires must finish perpendicular to a wall or ceiling face to be treated by the passive fire protection product. This should be considered at design stage as some fittings or pipe systems might require a larger penetration hole than a tested solution.
In a balcony situation with downpipes and deck drains combining, hidden in a soffit or exposed, details need to be considered for fall requirements, substrates, atmosphere and design. The intumescent material is not affected by atmosphere but if exposed to weather under a soffit a stainless steel fire collar will provide greater durability against the elements as opposed to a galvanised collar. Talk to Allproof if the selected system could cause concern as there are options available in this scenario.
A passive fire penetration for compliance with territorial authority needs to be a tested solution to the standard and be installed as per the manufacturer’s details. This may involve particular substrates, floor construction or floor depths, fixing type and penetration hole sizes. Allproof is constantly testing new passive fire solutions to keep up with ever changing materials and details. Allproof's specialist team are present on site and behind the scenes training installers and helping designers with selections.
When designing services in multi-unit dwellings early attention to the passive fire rating requirements will ensure compliance is achieved without having to revisit details. Building designers should work alongside passive fire engineers and manufacturers to offer the correct advice and products to achieve a successful, compliant solution.