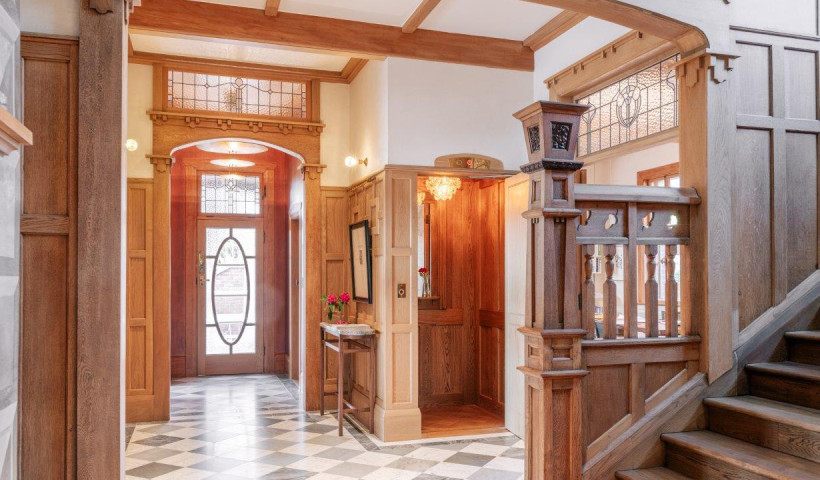
The pressure to reduce the construction industry’s contribution to landfills is one that has grown with the mounting waste. Powerglide understands this all too well and has adopted state-of-the-art manufacturing, inventory and delivery systems to reduce construction waste, so that remarkable design can be achieved in both an environmentally-friendly and cost-effective way.
This philosophy is inherent throughout the process, starting when Powerglide work with architects and builders to supply the required information for the design and consent process.
However, explains Powerglide CEO Mark Findlay, the real benefit of their systems come into play onsite, before and during installation. “Our development process is driven from the floor. Throughout the process we’ll communicate with the builder, making sure that we manufacture just prior to installation — meaning that we have accurate dimensions to build to.”
“We find that being a New Zealand company is a huge advantage," says Mark. "Being able to visit the site ourselves not only means that we can measure to fit, but it also ensures that we fully understand the build.”
What allows Powerglide’s late-to-build JIT delivery to accommodate the often-rapid shifting of building specs and timelines are their advanced systems. Powerglide can deliver within four weeks if required.
As well as the JIT manufacturing process, their Kanban ordering system, modelled on the famous Toyota Production System (TPS), ensures excellent stock management. “Kanban allows short lead times from New Zealand suppliers and minimal stock holding,” explains Mark. “This means we can make changes to parts without having to either scrap large amounts of stock, or wait until we have worked through the remaining units. We can also easily scale up and down if required.”
System and quality testing are also key to the process. “For our manufactured components, we have a double check quality assurance program. During the manufacturing process, if anything is flawed, the process is stopped, reviewed and solved then and there on the spot,” says Mark. “This means that no mistakes are repeated and no flawed materials slip through. This also minimises wastage.”
First and foremost, Powerglide provides high-performing elevators that not only complement, but also complete a home or light commercial design. However, Powerglide’s lean manufacturing systems allow unique, attractive design to be attainable in tandem with both cost and environmental considerations.