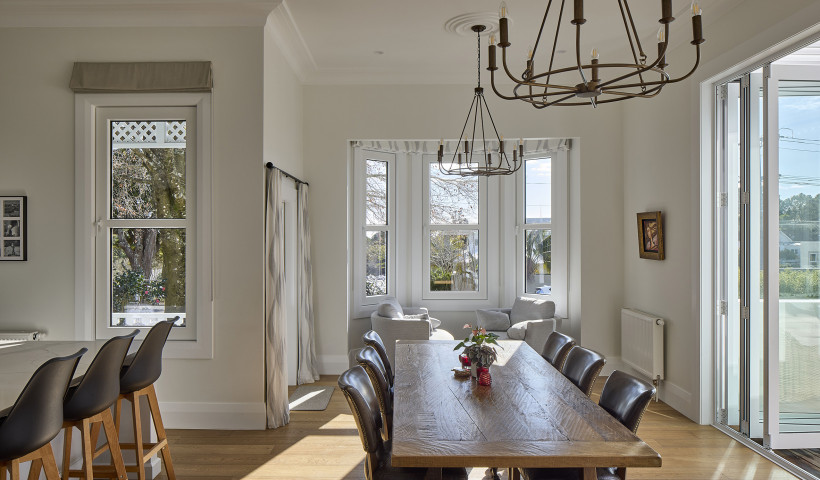
Previous company installations and capital works have had maximum eco-friendly features incorporated in them at the design stage, but existing processes at the company’s diverse operation at Te Rapa are continually under review as well. APL has recently taken more initiatives in packaging and distribution.
Paper interleaving of most aluminium extrusions is now carried out in the despatch process in lieu of foam-film protection which previously applied across the board. Wooden bases for cases of aluminium extrusions which were previously single-use items are now being extensively recycled back to APL from the manufacturer network and are repaired and reconditioned onsite for repeat use. APL’s manufacturing facility is also maximising re-use of cardboard boxes containing hardware which are sent out in quite high volumes to manufacturers. These are now protected in plastic bins and the empty boxes are recycled back to APL wherever possible.
APL’s powdercoating subsidiary, ColourWorks, has also bedded in a more environmentally benign pre-treatment regime for aluminium extrusions before they proceed through the company’s powder lines. Pre-treatment tanks are now chromium-free and this greatly simplifies onsite effluent treatment and disposal.
A comprehensive approach to sustainability has been taken in the design and construction of the new APL campus-style estate at Hautapu, where the first company facility housing APL and the glass plant, Architectural Glass Profiles (AGP), is under construction. This plant, designed by Jasmax, is being built to a high Green Star rating, which is unusual for an industrial building. All lighting in the factory operations and adjoining offices is expected to be powered from solar panels.
Over the next five years, APL is looking to relocate its operations to Hautapu from the four sites it currently occupies at Te Rapa. The new complex will be greener and more efficient across a whole range of sustainability metrics.