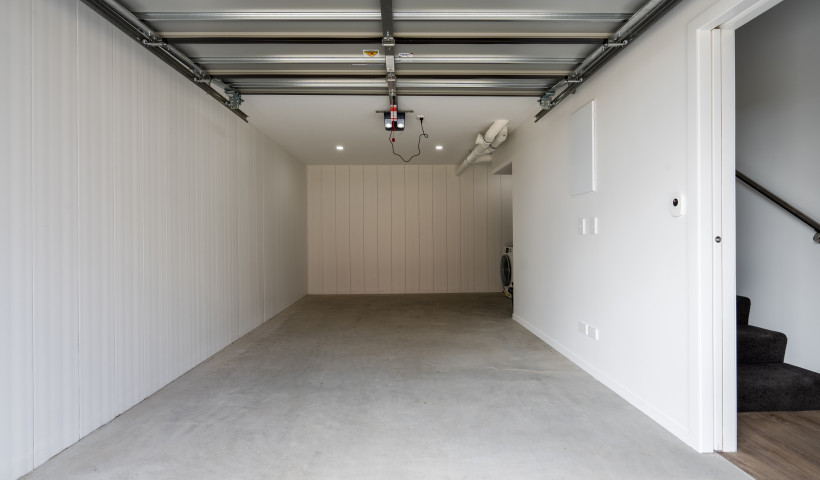
This new compost facility was constructed to manage the processing of waste from Gisborne’s wastewater treatment plant. The client, JUDDS Ltd, contracted Siteworx Civil to construct the facility within a very short timeframe to begin their contract on time. The AFS Rediwall permanent formwork system helped them achieve significant time savings in both design and construction to deliver a fit-for-purpose facility in just seven months.
“The time we had from winning the contract to the compost contract starting was around seven months, so not a lot of time to design and build the facility,” explains Blair Judd, General Manager of Siteworx Civil.
With the design and lead times needed for tilt panel construction pushing the project beyond this timeframe, the Siteworx Civil team had to find an alternative walling solution. In addition to the time pressure, the nature of the facility meant that specifying a corrosion-resistant material was crucial. Blair was familiar with the AFS Rediwall system, and after discussion with the AFS team, specified over 900m² of 256mm AFS Rediwall for interior and exterior walls.
AFS Rediwall is a permanent PVC formwork system featuring extruded wall panels which click or slide into place on site. Once panels are in place, steel reinforcements are installed and the walls are core filled to provide excellent strength and durability. The system’s modular nature, rapid assembly and low maintenance, corrosion-resistant wall surface made it a smart solution for the compost facility.
“The biggest benefits for us were speed of install, ability to meet timeframes, and the corrosion resistance” says Blair. “Because of the composting inside these structures, it's quite a corrosive environment. Using non-corrosive plastic formwork worked quite well for us on that front.”
Taking advantage of the modular nature of the system, the Site Worx Civil team saved significant time by ordering the walls while design and engineering was still being carried out. “With AFS Rediwall, we were able to have all the walls delivered to site while the plans were being finalised,” explains Blair. “This meant we were able to start building straight away with the slab and walls once engineering was complete, whereas if I’d gone with tilt panels, I'd have needed the design first, and to then get quotes based on the design, start panel construction, await curing and transportation to site.”
Use of AFS Rediwall also brought flexibility to the project where needed, such as the ability to trim the panels on site to make way for the sloping roof. “That ability to adapt the panels with minor changes on site was really useful,” says Blair. “I was able to have the 6m panels ready on site, and trim them down to get the slope of the roof once we had the final design.”
The building also had additional reinforcement requirements due to there being two structural floors to house all the piping needed. The AFS Rediwall system made it easy to install the additional L reinforcement rods, prior to pouring the wall. “Being able to add all the reinforcement in-situ was certainly easier than retrofitting into a cured panel,” says Blair.
The project wasn’t without its challenges with corefilling originally scheduled for the day Cyclone Gabrielle hit Gisborne. “We had to brace the wall and hope for the best,” says Blair. Even without the concrete core, the durable wall panels withstood the weather well.
Once the weather settled, installation was completed quickly and easily, helping the Siteworx Civil team deliver the facility on time. “We’re very happy with how it’s turned out,” says Blair. “AFS Rediwall was fit for purpose and suited what we needed to achieve — we probably saved about 6 months by using AFS.”