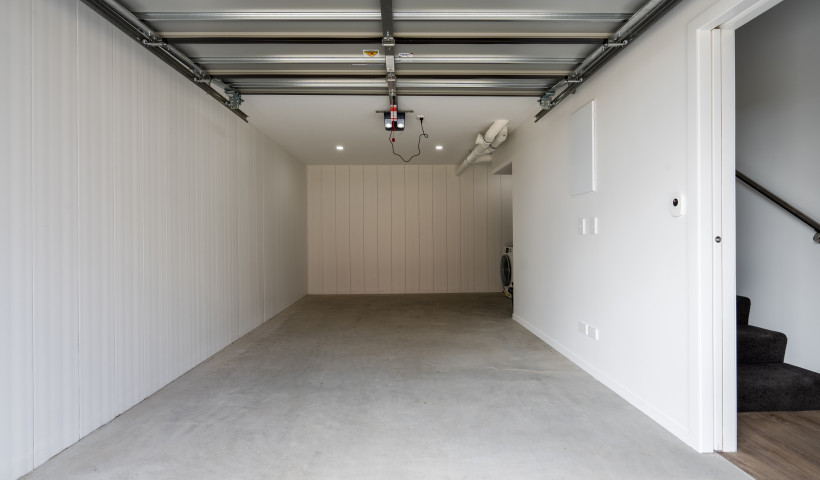
You are using an outdated browser version not supported by this website.
Click here to upgrade your browser
Logicwall Intertenancy Wall is a fire and acoustic-rated and load-bearing wall designed for medium-density projects including apartments, terraced housing, and retirement villages. Logicwall Intertenancy Wall consists of a steel stud frame with CSR fibre cement sheets bonded to each side of the studs, creating a wall panel that can be easily hand-installed onsite and core-filled with concrete. Depending on the fire, acoustic, and structural ratings required, Logicwall Intertenancy Wall is available in thicknesses of 150mm, 162mm, and 200mm.
Logicwall Intertenancy Walls are designed for use in multi-residential buildings such as:
If designed and installed in accordance with AFS technical literature, Logicwall complies with the following provisions of the NZBC:
B1 — Logicwall is an engineered system, with specifications provided by a certified structural engineer. Please refer to the Logicwall Design Guide for further information including design tables and limitations. There are also test reports available from University of Canterbury and Holmes Solutions outlining Logicwall's compliance with B1.
B2 — Once constructed, Logicwall does not contribute to the structural capacity of the wall which acts as a normal concrete structure. When used and constructed in accordance with the design guide instructions, the Logicwall system complies with B2.
C3 — Once core filled with concrete, Logicwall achieves a fire rating of at least 240/240/180.
C6 — Once core filled with concrete, Logicwall achieves a fire rating of at least 240/240/180.
F2 – Raw materials used in Logicwall are galvanized steel stud, Cemintel fibre cement board and Bostik structural glue. All materials are inert substances.
G6 — Only the 162mm thick panels and above meet or exceed STC 55 acoustic ratings for intertenancy walls. Additional strapping and lining can be used to increase the acoustic ratings on all wall thicknesses.
AFS New Zealand has been manufacturing and installing Logicwall on numerous projects nationwide since 2007. The Logicwall system is owned by CSR in Australia, where they have been manufacturing Logicwall for over 30 years.
AFS New Zealand manufactures Logicwall in Nelson, with offices in Nelson, Auckland, Wellington and Christchurch.
There have been numerous projects throughout the country that have utilised Logicwall as their Intertenancy Walls. Some of these projects include:
Logicwall Intertenancy Walls have been tested by Holmes Solutions to reduce the amount of reinforcing required in the panels. Download the design pathway for structural engineers.
AFS NZ manufacture and install permanent formwork systems for the multi-residential market throughout New Zealand.
Product Enquiries