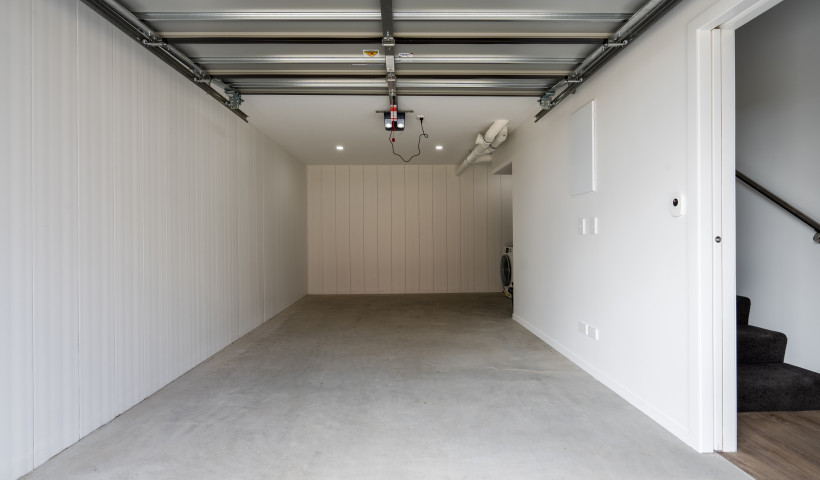
AFS New Zealand is proud to offer high-performance prefabricated wall systems that not only save time on site, but also contribute to reducing waste. Here’s a look at how their Logicwall and Rediwall permanent formwork systems can help minimise waste on site:
AFS Logicwall — a shop-drawn system made to the millimetre
Logicwall is a shop-drawn system that is ideal for multi-unit projects where it can be used for intertenancy walls, corridor walls, and lift and stair shafts. The digitised shop drawing process means formwork components are manufactured offsite to project specifications, with each panel labelled with a Panel code ID to simplify installation. With no need to cut panels to length or height on site, this speeds up construction and greatly reduces the amount of waste generated compared to traditional methods such as blockwork.
AFS Rediwall — a versatile system available in lengths from 0.6m to 7.0m
Rediwall is a PVC based lightweight permanent formwork system that is ideal for basement and retaining walls, and comes with a range of components that complement the panels. While not shop drawn like Logicwall, the system is available in specific lengths in a range of heights from 0.6m to 7.0m — ensuring there is a solution available for your project. This minimises offcuts on site, keeping more waste out of landfills.
Minimum concrete waste with in-situ pouring
Once the lightweight formwork components are in place, both the Logicwall and Rediwall systems are core filled on site. By pouring the concrete in-situ, the potential for concrete waste is effectively minimised.
Greater efficiency and fewer emissions for large projects
Logicwall and Rediwall are ideal for large-scale projects where they can improve efficiency. As the lightweight systems are installed by hand, they eliminate the need for cranes, and the related costs and emissions — all while providing time-savings through quick and easy installation. The walling systems have been specified on a number of large-scale projects across New Zealand, including Summerset retirement villages where AFS Logicwall has delivered efficiency in both design and construction.
Prefabricated systems that keep projects on track — and waste out of landfills
Ultimately, the efficiency of the Logicwall and Rediwall systems ensures faster construction than traditional blockwork and precast methods, helping to keep projects on track. The prefabricated nature of the systems, and use of shop-drawing and in-situ pouring of concrete effectively contribute to minimising waste on site.