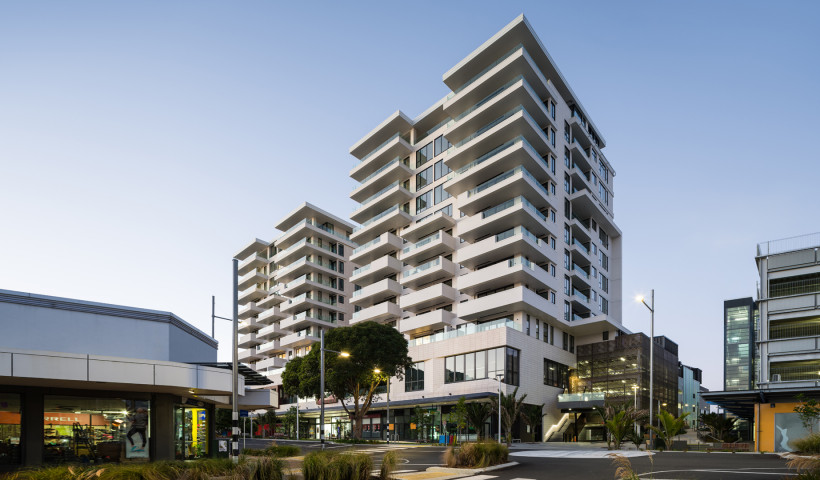
The homeowner had initially engaged Sang Architects for a limited renovation of his 2008 concrete blockwork home. However, when internal linings were removed, not only did they find very little internal insulation, but also extensive mould issues — particularly on the inside faces of external block walls and in the cold membrane roof cavity. This discovery led to a change in approach, with the homeowner deciding to undergo a full renovation aiming for Passive House EnerPhit Certification for the home.
EnerPhit Certification is a standard developed for refurbishments of existing buildings where it is not always possible to achieve full Passive House certification. Sang Architects working with Passive House Designer Jason Quinn of Sustainable Engineering, used the five key principles of Passive House design — ventilation, airtightness, insulation, high performance windows and minimise thermal bridging — to ensure better air quality and thermal comfort and to eliminate condensation and mould in the home.
To improve insulation and moisture management, Sto’s external insulation was an easy choice. “We naturally wanted to pursue external insulation,” explains Darryl Sang, Passive House Certified Designer and Architect, Sang Architects. “We know Sto’s long history, capability and quality, so it was a natural company to turn to. We’ve used Sto working on concrete previously so we knew their Sto system would be a great solution.”
The StoTherm+ Graphite EPS External Insulation and Plaster System was applied to existing concrete block walls — the graphite insulation panels increase R-values by up to 20% for better energy efficiency and savings. The system was finished with a StoArmat Render System, a synthetic, cement-free render system that provides protection and an extended life cycle for the building facade.
“We went with the 100mm thick graphite panels to meet insulation requirements and keep the house nice and warm,” explains Janice Au, Project Leader, Sang Architects. “And in terms of moisture management, the external insulation moved the dew point to the outside of the house, preventing future potential condensation or mould growth.” The StoTherm+ graphite panel external insulation achieved an R-value of 3.22, far exceeding project requirements.
Sto applicators, Plaster Solutions, did an excellent job of applying the system and managing the challenges of the project — which included levelling the undulated external wall face. “They had to do a lot of work to level out the external face of the building before applying the graphite panels and plaster systems,” says Darryl. “It went really smoothly because they knew what they were doing and how to resolve those issues.”
Janice and Darryl were also pleased with how they dealt with the detailing around the European joinery. “One of the good things about the Sto system being European designed is that they already have those details to cope with the junctions of passive house joinery,” says Darryl.
Utilising the expertise of Passive House Designer, Jason Quinn, particular attention was paid to remedying and reducing the effect of thermal bridges in the existing structure, other upgrades include a warm membrane roof and high-performance Passive House certified timber-aluminium joinery with double-glazed, low-E, low G-value (high shading coefficient) glass.
The focus on passive house design has been key to resolving performance issues and preventing mould and condensation from recurring in the future — with the Sto system playing an important role in the Passive House EnerPHit renovation. “Using the StoTherm system and placing the insulation on the outside resolved the issues we found with internal mould and dampness,” says Darryl.
The issues uncovered, and the fact they can occur in a home built to NZBC standards in 2008, illustrate the limitations of aiming for minimum compliance. “We can do a lot better and that’s what passive house is about,” says Darryl. “We model the whole house from an energy perspective and from a moisture and condensation movement perspective, designing and improving the whole performance of the house.”
A special thanks to builder Terry Bryers, Bruyere Ltd, who has been instrumental in the project, and to the client Bjorn Hilke for being part of the project team.
PROJECT CREDITS:
Passive House Certified Builder: Terrence Bryers, Bruyere Ltd
Passive House Certified Designer and Architect: Darryl Sang, Sang Architects
Project Leader: Janice Au, Sang Architects
Passive House Certified Designer/consultant for this project: Jason Quinn, Sustainable Engineering
Structural Engineers: Nick Baker, Richards Consulting Engineers
Sto Applicator: Adam Dobbie and his team at Plaster Solutions