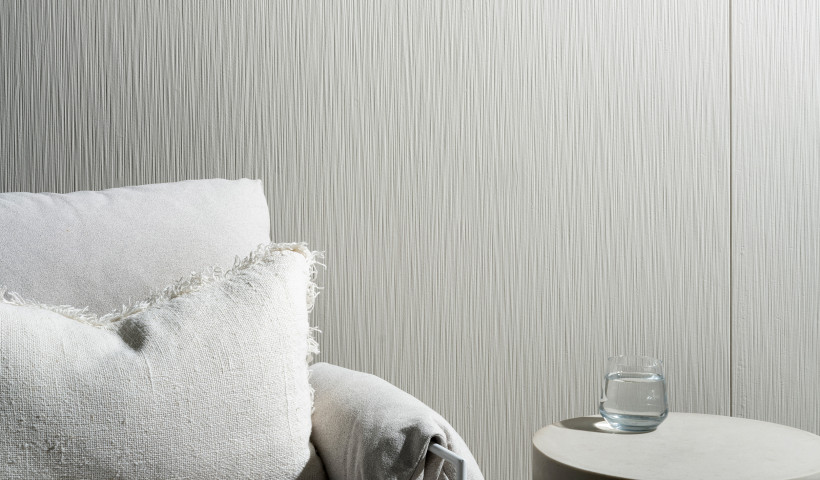
Project Overview
Built in 2000 at the height of deregulation, Sudbury Terrace is a multi-unit apartment complex in Parnell which was identified as a 'leaky building'. The building needed significant repairs to make it weathertight and compliant with present day Building Code requirements relating to fire and structural safety. Remedial work commenced in March 2015 and was programmed to take nine months to complete. However, major structural and fire safety defects were discovered beneath the cladding, adding an estimated further nine months to the project and taking the forecasted remedial cost from $5.7M to an unprecedented $10.2M.
The Solution
Andi Burrell, remedial specialist from ANOROC Remediation, specified James Hardie Linea Weatherboard and Titan Façade Panel as the main cladding of choice for this project. The products were selected in consultation with the client and following a detailed cost benefit analysis of cladding products to support their Financial Assistance Package (FAP) claim.
Burrell is experienced in commercial and technical due diligence of building materials — he has been doing this work since 1997. He selected Linea Weatherboard and Titan Façade Panel for their construction efficiency and competitive pricing.
Titan Façade Panel is robust, yet lightweight, making it quick and easy to install. It comes back-sealed for added protection from moisture and pre-primed on the face and edges ready for painting. Burrell says its quick installation made Titan Panel a cost-effective alternative to other monolithic cladding which would have required plastered joints and a full texture coat prior to painting.
The bold panelised look of Titan Panel contrasts beautifully with the classic lines of Linea Weatherboard. Linea Weatherboard was chosen for both its attractive traditional charm and durability. Manufactured from fibre cement, the product is low maintenance and has a 25 year product warranty.
Behind the cladding, Burrell and the client elected to use James Hardie Rigid Air Barrier (RAB) Board as a rigid wall underlay. RAB Board is a cost-effective pre-cladding product used in medium to high-rise construction.
"RAB Board offers a number of benefits compared to building paper," says Burrell. "It can be used to achieve structural bracing and fire rating between dwellings which is often difficult to achieve. When used in high wind zones, it is easier to install, and allows quick enclosure — speeding up the construction process, which was important on this type of project."
As the Project Manager representing the Body Corporate on behalf of the owners, Burrell says it was important to give something of value back to the owners, following the significant project delays and cost blowout. Fire safety was also a key factor influencing his decision.
Manufactured from fibre cement, James Hardie pre-cladding and cladding products are classified as non-combustible materials. They are also resistant to permanent water and termite damage, and when installed as directed, are resistant to rotting and warping.
Together the James Hardie cladding and pre-cladding products achieve a fire rating of 30 and 60 minutes, providing a safer environment for the owners.
Burrell is confident about specifying these James Hardie products for other projects, including a new build in Albany, and would recommend the products to others.
He also backs the James Hardie technical team, who he said provided excellent technical support throughout the project. "The technical team is approachable and passionate about the products. For me it was a no brainer to go with James Hardie — their products have always stood up."
Project Details:
Location: 80 The Strand, Parnell, Auckland
Project Type: Remediation
Project Manager: Andi Burrell, Principal, ANOROC Remediation
Featured Products: Rigid Air Barrier (RAB) Board, Linea Weatherboard (180mm), Titan Façade Panel