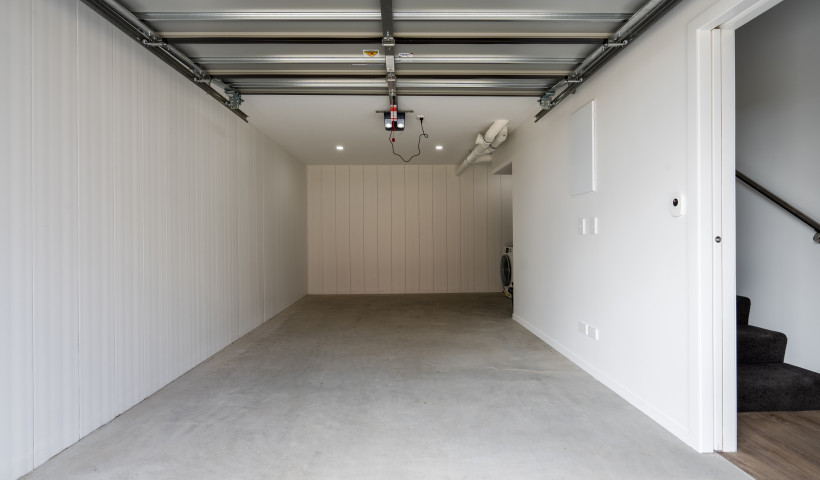
This 2000m² apartment block located in central Auckland offers 25 one and two-bedroom apartments over five storeys. Designed to ensure longevity and easy maintenance, the apartments feature high quality, durable materials. With construction occurring in late 2020 and early 2021 — a period of increasing supply chain delays — smart product selection was needed to keep the project on track. One product which met the brief was AFS Logicwall.
AFS Logicwall is a permanent formwork system that consists of a steel stud frame with CSR fibre cement sheets bonded to each side, creating a panel that can be hand installed on site and core-filled with concrete. The system is particularly suited to intertenancy walls, corridor walls, and lift and stair shafts, with thicknesses as low as 162mm achievable for intertenancy walls, depending on project requirements.
For medium density projects where space is at a premium, the Logicwall system offers significant space-saving opportunities. The system can be used to minimise internal steel work through a reduction of columns and steel posts compared to a lightweight structure, resulting in a clearer design space. And with stringent passive fire and seismic requirements met using a single slim intertenancy wall system, architects can maximise space in living areas.
The durability and slim design of Logicwall together with low lead times of 8 - 10 weeks made it a smart choice for the five-storey apartment project. “At the time when construction was happening there was a limited supply of precast concrete, so we wanted to minimise programme delays or issues with precast,” explains Craig Greig, Associate, Ministry of Architecture + Interiors. “Logicwall was recommended to us by the ECI contractor, who had used it on another project. We thought it was a good product with an advantage in terms of robustness for apartment corridor walls.”
The versatility of the Logicwall system meant that it could be specified for a range of walls in the building including intertenancy walls, stair walls and lift shafts, relieving supply issues. “The engineers had originally designed the building with precast structural walls, bracing and shear walls, but we managed to swap some of those out for Logicwall,” says Craig. “This gave us efficiency in terms of project delivery and no hold ups.”
By providing the structural, fire and acoustic performance required in a single system, Logicwall also helped to save time during the build. “There was no need to strap and line the product in corridors — it just needed stopping and painting. This reduced the number of trades needed,” says Craig. “The joints were recessed so walls could be flush stopped and given a paint finish. This gave us a hard wearing durable finish appropriate to the building use.”
AFS can help architects save design time, particularly when it comes to passive fire and seismic requirements, by providing shop drawings for the project. Craig appreciated the support from the AFS team throughout the design process. “The AFS team provided shop drawings done in-house by their team in Australia, and the local team were helpful in terms of design. They assisted the structural engineer as we wanted to get the product down to 200mm overall wall thickness.”
Ultimately, the use of AFS Logicwall helped the Ministry of Architecture + Interiors team achieve the passive fire, acoustic and structural requirements of the apartments and maximise living space, all while keeping the project on schedule. “We achieved the outcomes we wanted to achieve,” says Craig. “We thought AFS did a really good job. They’re friendly and approachable, have a fast turn-around, and are very helpful overall.”