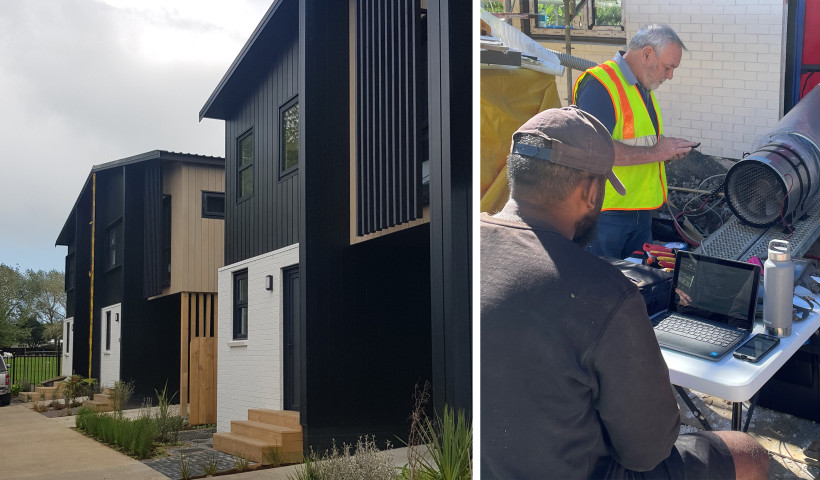
Located in Mangere Bridge, Auckland, this new terraced house development offers options for high-quality contemporary living with 15 homes ranging from two to four bedrooms. With an aim to meet the stringent requirements of Passive House certification, it was crucial for each of the homes to meet an airtightness level of 0.6 ACH (air changes per hour). When three of the homes were struggling to meet this level, the AeroBarrier air sealing system was used to successfully meet the airtightness requirements.
The ambitious project didn’t start out with Passive House Certification in mind, although comfort, sustainability and energy efficiency were always central to the design. The development had gone through design, resource consent and building consent, and construction had already begun on the first two homes, when the developer learnt about Passive House — something which changed the trajectory of the project.
“When the client became interested in aiming for Passive House for this project, we sat down and talked to them about the certification, the benefits and how to achieve it,” Respond Architects explain. “We then did the energy modelling for all 15 units to determine how we could achieve this.”
Developer Jasnish Gujral of Nest and Invest says it was the increased comfort and quality of living that convinced his team to make the shift to Passive House. “We said yes, let's upgrade our building and see if we can give buyers the best living conditions possible.”
Achieving Passive House wasn’t without its challenges — with foundations already poured, the architects needed to find a way to incorporate the changes required to achieve Passive House performance levels without increasing the overall height of the building. They also needed to switch to a higher performance ventilation system for improved heat recovery, and to increase airtightness of the homes to 0.6 air changes per hour. Initially they intended to achieve this airtightness with a membrane system — a challenging feat for the project builders who were new to both the membrane and Passive House builds.
“It was the builder’s first Passive House development and foray into any type of airtightness target, and their first time using the membrane,” Respond Architects say. “We detailed the building as well as we could but there were some junctions where they struggled to get to the standard needed — particularly in the midfloor, staircase and intertenancy wall.”
An initial blower door test on the first home failed to hit the airtightness target, leaving the team with two options: to manually detect and fill any air gaps or to look for an alternative solution.
“The team attempted to rectify the issues, plugging in every single air hole and we were still not 100% confident we could get the right results,” explains Jasnish. “It was at this stage that Respond Architects introduced us to Mark from Aero.”
Aero proposed using the AeroBarrier air sealing system to increase the airtightness of the homes — an automated system which uses a modified blower door assembly to pressurise buildings and seal hidden air leaks by distributing a low-VOC sealant which is directed straight to the gaps.
The AeroBarrier system was first tested on the first unit — which needed to achieve a result of 0.6ACH. Following a successful result, the system was then used on two more units that were struggling to hit the airtightness target. Completing the air sealing process took less than a day on each of the homes. Following the AeroBarrier air sealing all three units passed an independent blower door test, confirming the 0.6ACH airtightness result needed for Passive House certification.
“When it came down to the math, we could have had four guys spend another two weeks to rectify the build by manually plugging holes, or we could use AeroBarrier to resolve the issue in a day,” says Jasnish. “It was a no brainer.”
Using the AeroBarrier system helped to simplify the airtightness process, reducing labour costs and time on site to keep the project on track. “It was a learning process for the guys on site,” Respond Architects say. “They did all five units of that first block one after the other, and each one got better, but we got to the point that to avoid spending significant amounts of time trying to find these little leaks, it was going to be easier to use AeroBarrier.”
“This is one of the first multi-unit passive house projects in the North Island and it’s admirable that the client has done this,” Respond Architects add. “The whole project team has been great, including the builders on site. It was really valuable working with a team that haven't done this type of build before as I see they've recognised the value of stopping thermal bridging and air leaks, and have taken the time to understand the benefits of Passive House.”
Now in the final stages, and with certification on the horizon, this multi-unit project has been an ambitious learning curve — but one well worth it for the end result. The airtightness achieved has contributed to consistent comfortable temperatures in the homes. “Being Passive House, we notice the buildings are a lot more comfortable, and drier than our other buildings,” says Jasnish. “And once we turn the ventilation system on it will be amazing living there. Overall, we are more than happy.”
Project credits:
Developer: Nest or Invest
Architects: Respond Architects