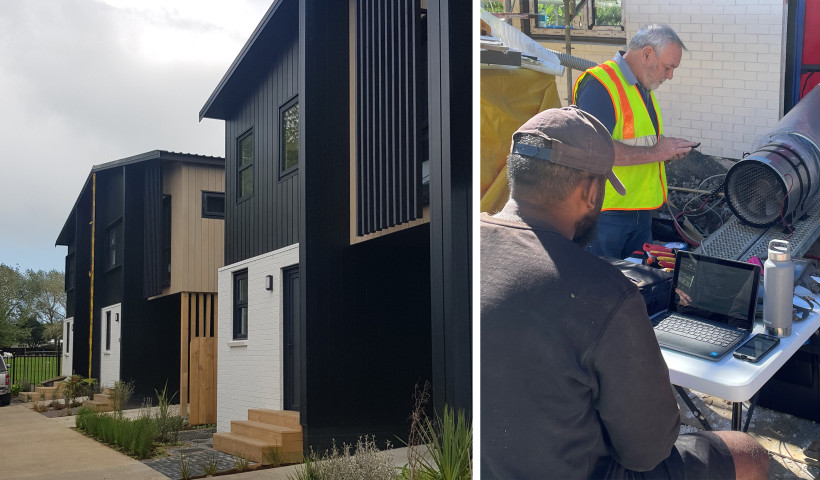
Located in Wai o Taiki Bay in Auckland, this medium density rental development features three 107m² townhouses which were designed to aim for Homestar 6, version 5. Ensuring airtightness of less than two air changes per hour (2 ACH50) for each of the three homes was an important step in helping the homes to achieve the lower space heating demands required under Homestar. Specification of the AeroBarrier Air Sealing System ensured accurate measurement of airtightness, efficient sealing of air leaks, and an impressive end result of between 0.76 and 1.2 ACH50 for each of the three homes.
Initially, the homes were designed as standard under 3604, but after learning about Homestar the client decided to aim for Homestar 6 to futureproof the homes and increase the overall energy efficiency and sustainability of the development. With the need to bring the original design up to Homestar 6 standards, Nuline Homes, the contractors for the project, contacted Environmental Building Services Providers, BXG, for advice.
“The homes were not designed for Homestar from day one, so when it came to design, it was a retrofit style airtightness model,” explains Nick Allan, Builder and Director, Nuline Homes. “We found that airtightness membranes didn’t quite suit the project, so needed to look at alternatives.”
Environmental Building Services Providers — The Building Excellence Group (BXG), who carried out the energy modelling, had recently learnt about the AeroBarrier Air Sealing System — which launched in New Zealand in 2024 following years of successful use overseas. The AeroBarrier system uses a modified blower door and fan assembly to pressurise the building envelope as Aero’s patented software system accurately measures air leakage. Once an initial measurement is taken, a non-toxic, low VOC, water-based sealant is then distributed throughout the home, following the flow of air currents to effectively seal any air leaks — with Aero’s software monitoring the effectiveness in real time.
The system offered a way to accurately measure and increase airtightness, without the need to modify the wall build-up, making it ideal for the project. It was specified in conjunction with a mechanical ventilation heat recovery system, combining airtightness with moisture management to ensure energy efficiency, durability and healthy air quality.
The air sealing process was quick and straightforward with the Aero team handling everything from set-up, air sealing and clean-up, through to providing a final test certificate for each of the three dwellings. “The Aero team were great,” says Nick. “They showed us exactly how the product was working, and the results right the way through, so we could see where it started and finished, and how much impact the AeroBarrier had, and they left us with a nice clean and tidy site that was good to go.”
Using the AeroBarrier system provided a quick and simple way of achieving airtightness, and eliminated the risk that can come from using a vapour membrane — which depends on correct installation to achieve airtightness, with the results only revealed after installation.
“The speed was a big benefit,” says Nick. “It was done post-GIB installation, so you can have a normal construction methodology — no special tapes or barriers or installation methods other than letting the product do its thing. They were done within a day for the three houses, so it was a fast process for the construction schedule.”
And importantly, the process resulted in reducing air changes per hour to between 0.76 and 1.2 for each of the three houses. “It delivered the ratings we needed to get down to for Homestar, that was obviously a big benefit,” says Nick.
This was the first project where BXG had used AeroBarrier, and they were pleased with the results achieved and ease of the process. “It was very quick and painless,” says Liam Pugh, Senior ESD Consultant, BXG. “Because it's largely automated, it reduced the pain of running around with a smoke gun to find tiny little air leaks, which can be very time consuming.”
“I’m quite impressed at this stage," says Liam. “Several of these dwellings started off with pretty high air change rates. Unit 3 was already fairly airtight at 3.46ACH, which was great to see as an initial reading, but another was hitting 6.04 air changes per hour which is the equivalent of up to about 460L/s of air movement in and out of the house, or about a 428cm² hole in the house. Homestar has assumptions that all houses would be achieving under 5 air changes per hour, so that was quite high, but is pretty typical in New Zealand construction. We managed to get those down based on the positive pressure test to 0.82 and 1.2 air changes per hour — which is the equivalent of 91.1L/s of air movement or a 150cm² hole. We were able to hit all our Homestar targets based on these preliminary airtightness results."
Liam notes that the MHRV system was another key element of the airtight homes — and something architects need to consider when increasing airtightness. “If leakage is reduced then other means of supplying fresh air should be considered to ensure sufficient levels are supplied to the occupants, maybe through passive vents or a balanced mechanical system with continuous supply and extraction.”
The increased airtightness of these new rental homes will translate to much lower energy bills for tenants. “Homestar houses require a space heating demand of less than 40kw hours per metre square per year,” explains Liam. “These homes started at 45 - 47kw hours, and then following air sealing that had dropped that down to 37 — that’s a reduction of 16 - 22% in energy demand used for heating across the three units, to maintain a temperature of 20 degrees celsius across the homes.”
Ultimately the choice to use AeroBarrier has kept the project simple for the builders, while resulting in the airtightness and energy efficiency for the homes required for Homestar. “AeroBarrier achieved exactly what we needed to achieve,” says Nick. “We got down to the right amount of air changes for Homestar 6. We couldn’t ask for better.”
To learn how the AeroBarrier system can help you increase airtightness on your projects, get in touch with Aero.