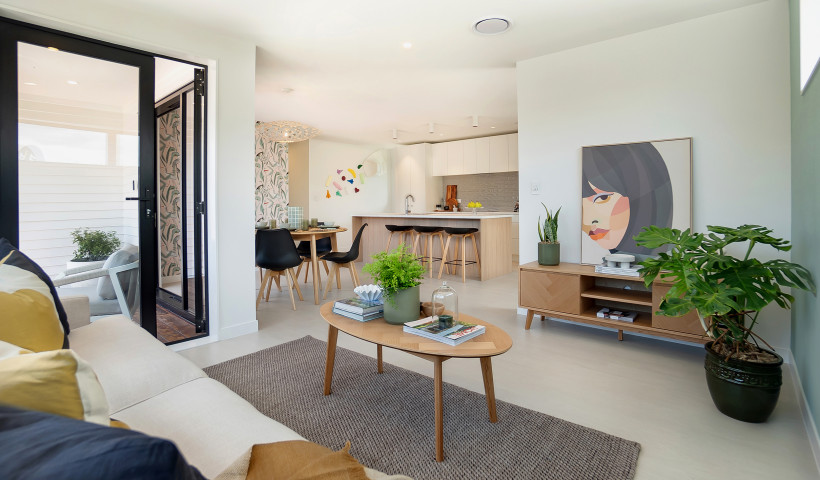
With an aim to test new methods of increasing airtightness and energy efficiency, Fletcher Living recently trialled the AeroBarrier air sealing system on a new build in Auckland. The home was designed with a mechanical ventilation system and built to Fletchers standard specifications, giving the team a chance to test the effectiveness of the air sealing technology on a standard build — with the aim of bringing airtightness down to under 1 ACH.
“We are always interested in testing products coming into the New Zealand market, especially where they improve the performance of the home,” says Ben Field, Building Performance Lead, Fletcher Living. “Our particular interest in AeroBarrier is that lowering a building’s air leakage helps to reduce operational energy consumption by building a home that requires less heating and cooling to account for air lost through small leak points in the thermal envelope.”
AeroBarrier is a tried and tested air sealing system that has been introduced to the New Zealand market by new Kiwi-owned company, Aero. The system involves the use of a blower door test to first assess the level of airtightness in the building, followed by distribution of non-toxic water-based sealant using that same blower door technology to pressurise the space and effectively identify and seal any air leaks. The system is a smart option for enhancing airtightness in new builds and renovations alike.
“One of the benefits of AeroBarrier technology is that the process can be carried out at any time after the building is closed in, i.e. cladding and linings are installed,” says Ben. “Because we build new homes it made sense for us to carry our air sealing once plasterboard linings were installed and stopped.”
For the Fletcher Living pilot, the AeroBarrier process was very straightforward. The Aero team was on hand to manage the air sealing on the day, which involves prepping the space, setting up the blower door and spray stations and cleaning up once air sealing is complete — allowing work to resume within 30 minutes.
“The process itself is quite simple; the building’s windows and doors are masked internally then a blower door system is set up — we set ours up on the internal garage door. AeroBarrier set up their application equipment inside the house, and then the house is pressurised,” explains Ben. “Once initial pressure measurements are complete, the AeroBarrier product is released into the internal air space and sealing begins immediately.”
A key advantage of AeroBarrier is Aero’s specialised software which allows you to set your target airtightness level and monitor progress in real time. This gives architects and builders peace of mind that they will meet their required airtightness.
“It was great to watch air sealing occur in real time,” says Ben. “The monitoring system runs continuously throughout and the reduction in air leakage can be viewed in real time as opposed to traditional wrap then test processes.”
At the end of the process, a final blower door test is run to verify the results, and a Certificate of Completion is issued, confirming the exact level of airtightness achieved. The AeroBarrier Certificate of Completion is accepted by the NZGBC as proof a house has achieved the ACH50 result required, making it a simple and cost-effective option for meeting and verifying requirements for Homestar projects.
In the Fletcher Living pilot, the end result was a 90% reduction in leakage, which will result in a much greater level of energy-efficiency for the home.
“The end result was exactly what it was meant to be, which is always a great result for any builder,” says Ben. “Our pilot house reduced to an ACH of 0.85 which is an impressive outcome, especially given the ease of installation. The pilot house is not yet occupied but we expect to see measurable reduction in energy consumption for its future occupants.”
The testing of AeroBarrier’s technology is part of wider initiatives taken by Fletcher Living to enhance the sustainability and energy efficiency of their builds. “Over the past three years, Fletcher Living has done the hard yards to develop a blueprint for future sustainable and energy efficient housing and has led a low carbon, low energy, low water use pilot called LowCO,” says Fletcher Living Head of Sustainability, Nicola Tagiston. “We are committed to enhancing energy efficiency. By reducing the need for heating and cooling, we can help our customers enjoy lower energy bills.”