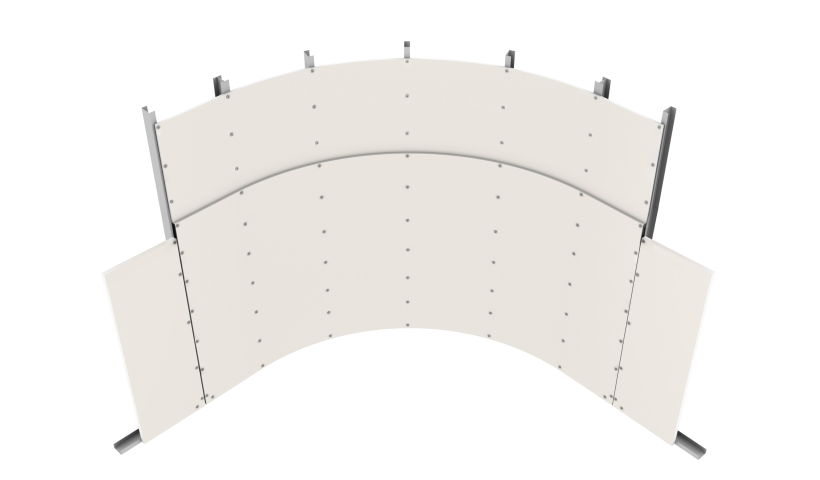
With the rise in terrace home construction, the new GIB Intertenancy Barrier Systems for Terrace Homes have been designed to provide an improved NZBC compliant separating wall between attached dwellings. Technical literature is available now for download from the GIB website along with CAD and BIM details, or specifiers can call the GIB helpline to order a physical copy.
GIB Intertenancy Barrier Systems
The system consists of a double timber frame wall with a 25mm thick plasterboard barrier between the frames. The primary fire resistance is provided by the central GIB Barrierline plasterboard barrier, with the GIB wall linings contributing to some extent. This allows the wall linings to be used for structural bracing and to incorporate untreated penetrations. The basis of the acoustic performance is a double cavity system. This provides isolation from both airborne and impact sound. Insulation in both cavities is used to provide thermal comfort and noise attenuation levels and allows certain services to penetrate the wall linings.
Benefits:
High performance
- GIB Intertenancy Barrier Systems achieve between 61–68 STC, well in excess of the New Zealand Building Code minimum for intertenancy walls (clause G6).
- 60 minute FRR
Cost effective
- Comparing total cost of the system (including labour, foundations, equipment) GIB Intertenancy Barrier Systems are some of the most cost effective in the market. Compatible with GIB Bracing systems and GIBFix Framing System
Narrow footprint
- Maximise the available tenancy area of each unit.
Lightweight construction
- No need for additional/specific foundation designs.
- Particularly attractive in seismic areas.
Great buildability
- No specialised sub-trades for installation
- No specialised equipment like cranes
- Easy and fast to install
- No need to fire seal most standard electrical or plumbing penetrations that pass through the wall linings, these penetrations do not degrade acoustic performance.
- Often results in faster council inspections due to fewer problems with penetration design
- No need to take the wall linings up to the roof space
Performance and durability
GIB Barrierline has a specialised formulation with a water and mould resistant core allowing GIB Barrierline to be exposed to the elements in-situ for up to 12 weeks — giving specifiers flexibility in construction. 16mm GIB Fyreline used in the roof cavity can be exposed in-situ for up to four weeks. Both products must stay dry and protected until installed. In addition, they are thoroughly tested in the lab and in construction trials specifically for New Zealand conditions. Testing has included extended element-exposed durability testing, freeze-thaw testing and soakage tests.