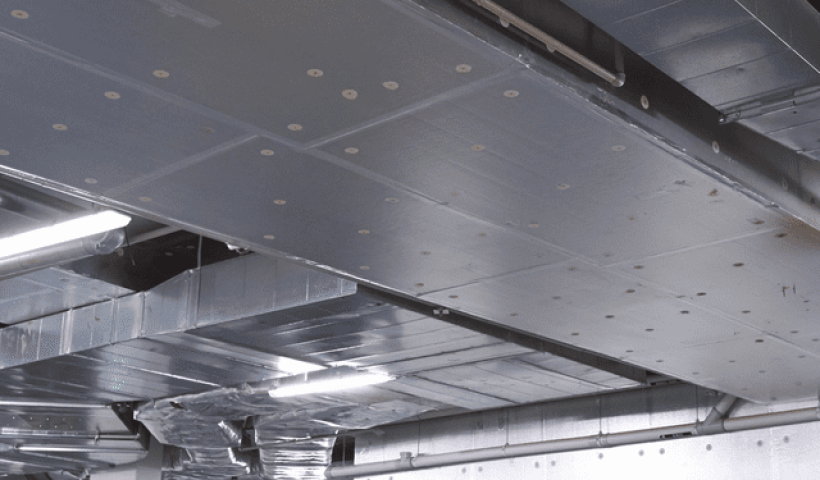
When we hear the word carbon nowadays, we hear a lot of companies ‘talking the talk’ on slashing their emissions. Unfortunately, what we do not hear in many cases, is how exactly and when these emissions are going to be cut.
When it comes to carbon reduction, Kingspan Insulation New Zealand is ‘walking the walk’. With a set of ambitious targets to reach under the ‘Planet Passionate’ long-term sustainability strategy, the business is reducing actual carbon year on year. The first target that Kingspan has set itself is ‘Net-Zero Carbon Manufacturing’ at their Auckland site by 2030. This means that all operational energy that goes into producing their products must be from renewable sources and produce zero carbon.
To meet this target, the business switched to 100% certified renewable electricity in 2022. This transition will see the scope of two emissions (CO2e) cut by approximately 142 tons per year. The second step to achieve this target is the transition to electric forklift trucks. Kingspan's Otara facility already has achieved 25% of this target. This figure will rise to 50% by the end of 2023 and the entire fleet will be switched to electric by the end of 2024, meaning the site will be net-zero carbon manufacturing.
Another ambitious challenge relating to carbon reduction that they have set themselves is to transition to ‘zero-emission vehicles’. By 2025, 100% of annual company car replacement leases’ must be electric and by 2027, the entire Kingspan Insulation New Zealand fleet must be electric. This is an important step in the reduction of carbon from their scope 3 emissions.
Kingspan are very much aware that they simply cannot draw the boundary line at operational carbon. They are also on a journey to reduce the embodied carbon of their products and limit any environmental impacts. To do this, they are taking a two-step approach which firstly consists of performing ‘Life Cycle Assessments’ and ‘Environmental Product Declarations’. They published their first EPD covering several of their Kingspan Kooltherm products earlier in 2023. This step allows them to view the entire lifecycle of their products, find any environmental impacts and understand where any carbon is derived from. Once they have understood the product lifecycle, they find ways of reducing any environmental impacts. Some of the ways they are doing this are, for example, finding more local raw materials supply, using recycled materials, and looking for bio-based alternatives. In their Auckland plant, they have successfully implemented a programme to recycle all synthetic underlay manufacturing waste (i.e., Covertek, Watergate Plus and Thermakraft 220) and convert the waste back into useful material. Year to date their Auckland plant’s landfill avoidance performance is averaging 66%, which means more than half of the plant waste has been diverted away from landfill.
Finally, they are also demanding a 50% reduction in product CO2 intensity from their primary supply partners by 2030. To reduce carbon footprints, a joined-up approach is needed, and this target will drive the upstream emissions from Kingspan's supply chain down.