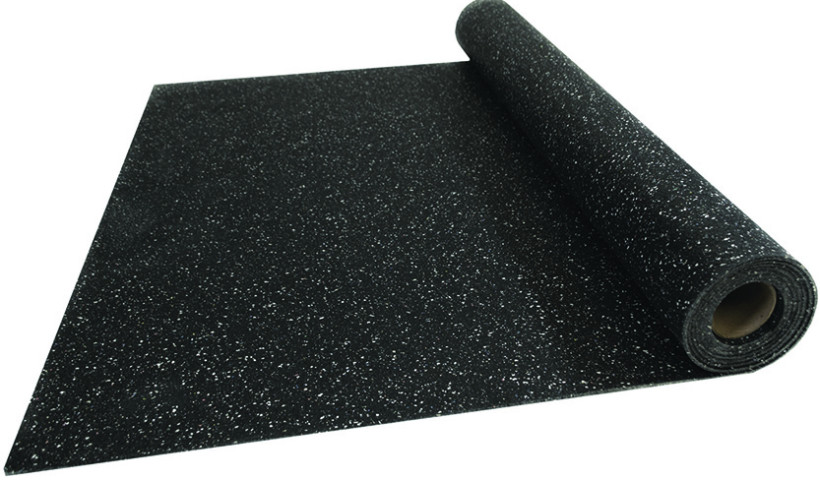
The NZ Building Code has always required waterproof finishes in these areas but most recently the E3/AS1 has been amended to require impervious finishes that are easily cleaned, have sealed or coved edges and are absent of gaps or cracks.
Kitchens, bathrooms, laundries and toilet facilities have always called for stringent sanitary conditions and impervious surface flooring finishes in open plan areas; these must extend at least 1.5m from all sanitary fixtures and sanitary appliances. This includes showers, baths, toilets, sinks, dishwashers and washing machines, even those in domestic laundries in garages.
This has never been an issue but now the onus is on installers of floating flooring to ensure they follow installation instructions to the letter, to ensure compliant water resistance particularly around perimeter edges. Also, it is important for product importers to communicate clearly the solutions which have been delivered successfully in overseas builds and local builds, without issue.
The Amendments to E3/AS1 state, floor finishes exposed to water splash must be installed in a manner that prevents gaps or cracks within the finish and at any parts of its perimeter or the surface is sealed with a suitable durable coating.
In the past, acceptable solutions included an integral waterproof sheet material such as polyvinyl chloride with sealed joints and additional sealing or coving at edges where there may be water splashes. Ceramics and stone tiling with waterproof grout or sealed concrete floors have been traditional choices.
Now, other flooring finishes can satisfy this impervious performance criteria so long as its installed without cracks or gaps and/or the surface is sealed with a suitable durable coating.
Woodland Lifestyle’s flooring satisfies this criteria due to their water-resistant surface finishes and wet area installation systems which resist water ingress around the edges.
The surface technology of Woodland Lifestyle's products is impervious and easily cleaned through a number of methods including heat-cured melamine, PVC and polyurethane resins. Maintenance of the surface is easy care with a damp mop.
Woodland Lifestyle’s flooring utilises world-leading locking systems such as Uniclic and 14F’s drop-lock technology. These highly engineered systems provide an extremely tight glueless joint inhibiting the possibility of any moisture creeping through without additional sealing.
Combine this with their wet area installation method utilising a foam rod and transparent silicone at the perimeter of the room and you have a finished floor impervious to water spills and splashes.
An elastic, waterproof and transparent paste is applied to a compressible foam strip with an 8 to 10mm diameter utilised at the perimeter of any flooring installation. The foam is pushed into the expansion joints and sealed with Silicon. Silicon is applied around the edges of skirting boards to avoid the ingress of any water.
This system can also be utilised at mid-floor expansion joins, the wall base, door frames and any pipes or plumbing.
By following clear installation and maintenance instructions, Woodland Lifestyle’s warrantied flooring ranges can continue to be specified in wet areas and enjoyed for many decades to come.
Woodland Lifestyle recommends including their alternative solution document when submitting a project to council — find the alternative solution document here.
Check out detailed Product Technical statements and Installation Instructions for Woodland Lifestyle floors on the Woodland Lifestyle website.