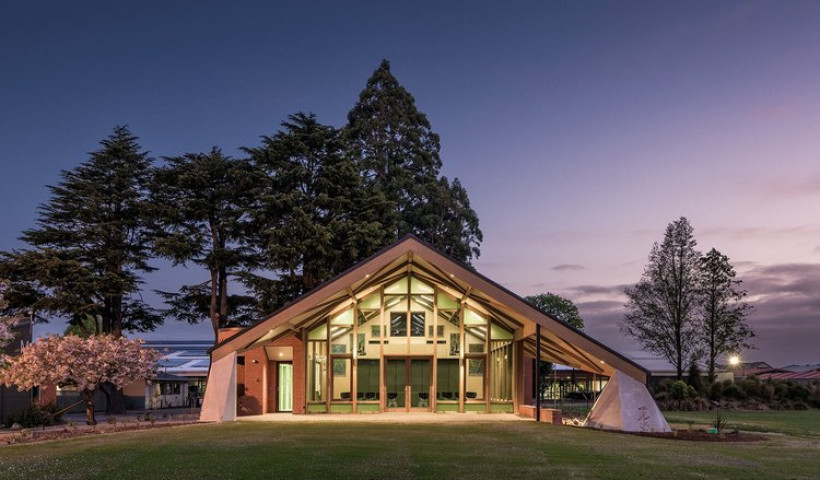
At Techlam, prefabrication of products at their manufacturing facility in Levin has become more and more popular over the last few years. Now with Covid-19 slowing on-site work, it is a great option to look at for reducing time spent on site. Installing prefabricated components is quick, easy and reduces on-site waste.
Techlam recently supplied components for the Hornby Working Men’s Club. The off-site manufacturing of this project saved the client a lot of time and potential waste on site, and along with other prefabricated elements from different suppliers, the project was assembled quickly with accurate site tolerances.
With the main truss fully prefabricated with intricate detailing all done in the plant, the final truss has only glulam showing, with all connections hidden. This was shipped to site ready to install. The time and waste saved by carrying out this work offsite was immense. It meant the glulam could arrive at site and be lifted into place efficiently, quickly, and accurately.
In NZ on-site construction waste is one of the single largest sources of waste. By prefabricating components, Techlam can reduce overall waste on site. Any unavoidable waste can be disposed of responsibly, taking the environment into account. Carrying out prefabrication in the Techlam plant ensures that when products are delivered to site, they can be ready to install with less time, less tools, less brainpower, less wastage, and less hassle for everyone involved.
As a responsible manufacturer, Techlam is dedicated to providing reliable solutions that benefit all stakeholders. Off-site manufacturing is an efficient and cost-effective way of providing a reliable solution that benefits everyone involved.
Location: Christchurch
Client: Hornby Working Mens Club
Architect: RM Designs
Engineer: ENGCO
Head Contractor: Contracts Construction
Products Used: Glulam Truss, Portal Frames & Purlins
Date: 2020