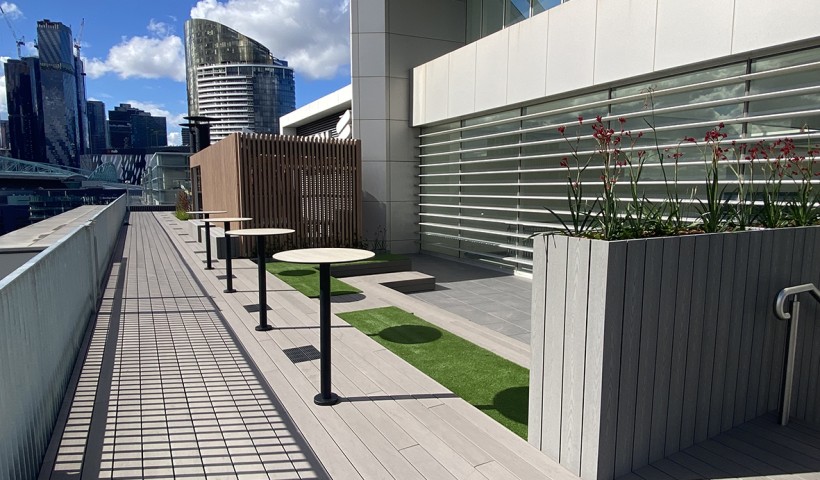
Eliminate the liability issues and headaches by avoiding the following:
1) Insufficient Airflow
Any structure placed on top of a membrane needs sufficient airflow to promote deck health and reduce the chance of mould and mildew. 12mm clearance around the perimeter of a deck does not constitute good air-flow.
2) Difficult or no access to gutters and downpipes
Any product installed over a membrane must have the ability to be removed easily to provide maintenance access to gutters and downpipes to remove debris and check for blockage.
3) Relying on wedged timber subframes
The purpose of a subframe is to provide a solid, stable structure to fasten decking boards to. Pine joists ripped into wedge shapes do not hold shape nor offer a solution friendly to the membrane its sitting on. Pine is incredibly unstable during absorption and evaporation of moisture when used as a floating structure with no strapping, bearers or piles to restrain it.
4) Difficult or no access to inspect membrane
Access to membranes should be quick and easy without the need to lift heavy waterlogged panels. Even "small removable" panels once waterlogged can be extremely heavy to lift without an army of builders. Do your client a favor and ensure the design solution includes easy removal of the decking surface.
5) Materials permanently fixed to subframe
Do not fasten decking boards with nails. If a deck has to be uplifted, timber decking boards end up being expensive kindling once lifted if they have been installed with nails.
6) Re-engineering required
All too often, especially on reclads and leaky buildings etc where structural tiles are being considered for use over membrane, its only too late to find out the building would require re-engineering to withstand the significant amount of extra weight or clients are forced to consider expensive structural ceramic tiles.
To experience QWICKBUILD®, the revolutionary decking system for over membranes and talk to the decking experts call 0800 77 88 77 or visit www.outdure.com.