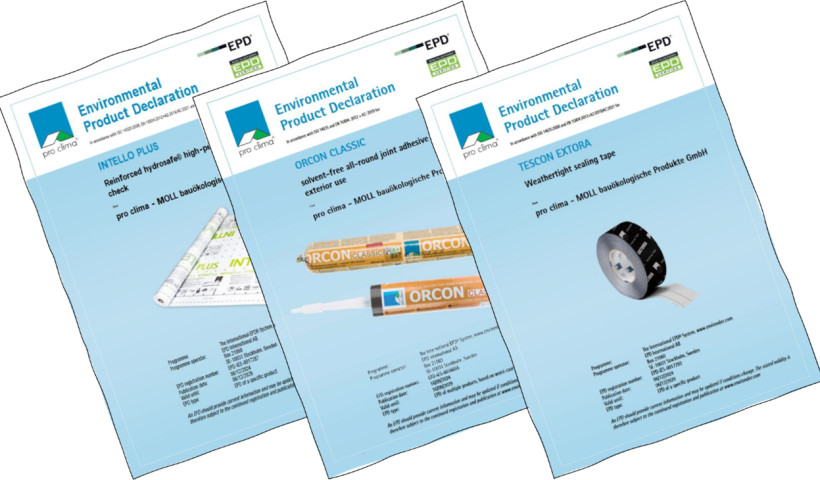
A house built to the NZ Building Code is the worst building you can legally build — unfortunately most Kiwis don’t know this.
pro clima NZ support homeowners, builders and architects that want to build better. They enjoy seeing innovation as they help, promote and support the industry to exceed the norm and make a difference.
Driven by her passion for the outdoors, Carolin Friese called Queenstown her home in 2012 after finishing her architecture studies in Germany. She set out to learn all about the Kiwi way of building before opening her own practice (Carolin Friese architecture) with a focus on highly energy-efficient homes.
Together with her partner, she purchased a section in Bob’s Cove, west of Queenstown, that is nestled in a native beech tree forest. Having completed the Passive House course in 2019, Carolin started to design their own low-energy home that would be both comfortable and functional.
With the house currently under construction, their journey of building a high-performance home in an area with very low sunlight hours during the winter months has been full of its challenges, but a strong collaboration between the designer and the building team at Goodwill Building has proved to be valuable in finding new innovative solutions to reach the desired result.
It’s very important to have the intended outcome visualised and communicated when designing a new home. To build a thermally efficient, high-performance home, the designer should ensure that the performance of the design is verified by using an appropriate tool, such as the Passive House Planning Package (PHPP) for example. The thermal modelling helps to understand the requirements specific to the site, such as outdoor climate and shading, as well as giving feedback regarding the required level of insulation to achieve a high-performance house.
It is also important that the building envelope forms a continuous weathertightness, airtightness and insulation layer while identifying and reducing thermal bridges. Major junctions such as window to wall, roof to wall or wall to floor require high attention to detail when it comes to selecting materials to reduce thermal performance loss.
Windows are the weakest thermal element and it pays to consider the use of good quality windows suitable for the geographical location, including awareness of shading and solar gains to avoid overheating.
Combining a continuous airtightness and vapour control layer (along the floor, walls, windows and ceiling) with a balanced MHRV System creates a draught-free and well ventilated environment. It also enhances the performance of the insulation layer by preventing damp air from entering the structural envelope. Verification of the performance of the airtightness and vapour control layer can be done with a WINCON fan during construction. This is done before the first Blower Door test to check for any leaks. Generally, there are two Blower Door tests, one after airtightness layer is installed and one on completion of construction.
Carolin has applied her knowledge to their home while prioritising function and performance over complex form and an expensive fitout.
Internally, the house has a central living and kitchen space with a bedroom and bathroom arranged on either end. This allows for flexible usage of the spaces, as a guest room or an office, as well as being able to shut one end when not in use. The bathrooms are accessible from the living room but can also function as private ensuites. The loft is the heart of the building, facilitating breathtaking views towards Walter Peak as well as incorporating a sunny window seat.
Structurally, Caroline followed the approach of less is more when it came to timber framing and managed to design a double storey building with framing at stud centres of 600mm — without any dwangs or big lintels. Every element has been carefully considered in terms of its use and location utilising the internal and external 45mm cavity for additional structural elements such as a continuous midfloor stringer and structural battens for the cladding. This construction approach allows for an incredibly easy way of installing the airtightness and vapour control membrane without any internal walls in place that would normally create junctions to the exterior walls, roof, and floor. Furthermore, it facilitates any floor plan changes with ease making it future proof for generations to come. German triple glazed timber windows, a balanced mechanical heat recovery ventilation unit as well as an airtight envelope were non-negotiables when designing and pricing the house.
It can be simple to construct a warm, efficient, low-energy building with good vision, careful planning and a team that is able to collaborate successfully.