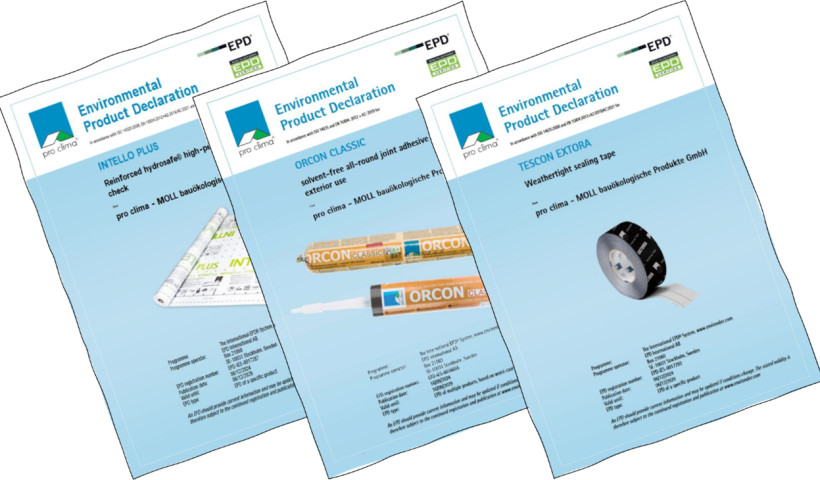
When Bob started building 63 years ago, the build process was a little different. Rimu framing was brought out of the West Coast; a jumble of material, ungauged, rough-sawn in a variety of dimensions. It was dumped on site and the carpenters did their best. Bob would check out the bottom plates so the studs would all end up at the same height. Kerosene cans were filled with concrete and used as piles, or maybe Oamaru stones were placed, and the bottom plates were laid on those. As Heraclitus, the Greek philosopher said, “Change is the only constant in life.”
Looking around this site today in Opawa, Christchurch I can see a very different story. The design is heritage, but the techniques and materials are the latest methodologies in New Zealand building industry.
Glenn Murdoch of Theca Architecture designed the home based around the customers’ connection to the past, and their love of the garden and growing their own vegetables. The garden has a pump track and the owners love the outdoors. The traditional 1920’s styling is not typical of modern airtight homes and its form factor does not lend itself to a Passive House. But the house performs well and meets the needs of the client wonderfully!
Cam and Bob Huxley are a father-and-son team building a high-performance home. It uses the latest technology in triple-glazed UPVC windows, mechanical heat recovery ventilation (MHRV), and airtight wall construction. Outwardly, the design is not what you’d expect to see; exposed rafters, brick veneer and scrolled facia on the gable end. But inside it is a different story.
The primary structure is 140mm laminated veneer Lumber (LVL) filled with high-performance glass fibre insulation. However, you can’t see that now because there’s a vapour control layer in the way. The INTELLO Intelligent Air Barrier performs a few important functions and covers all the internal faces of the external walls. It also lines the ceilings. Effectively, this high-performance vapour control layer manages the internal moisture generated by the occupants, cooking, showering etc. It also manages the airflow or draughts. It is not in the building code, but is it necessary? International best practice thinks it is, and so does Bob.
Bob would like to see all houses be better insulated, use thermally broken windows, more insulation in the walls and roof spaces. There’s no need to build homes that need to be heated all day. Cam hopes all homes will one day be built to a higher standard of insulation utilising panelisation and pre-fabrication. He’d also like to see the use of untreated timber in the internal structure.
This is their first high-performance home. Cam was awarded a scholarship through Pro Clima NZ to attend the Passive House Tradesperson course. He had been doing a lot of self-studies prior to the course and passed the test with great results the first time. No easy task! When the opportunity to build this house came up, he jumped at the chance.
Embracing change transforms the built environment. We have long understood the physics of thermodynamics, we’ve been to the Moon, put robots on Mars, have hot tea in flasks… Why should we be designing homes that require double figure kW to maintain a comfortable indoor temperature? Bob and his son Cam welcome the changes to H1 but think they don’t go far enough. There’s a belief in the industry that the builders are holding back the changes. I don’t see that. I see guys and girls doing their best to build warm, dry, healthy homes that will last a hundred years or more and hardly need any heating for the length of their lives.
Cam explained that if the money is invested upfront for the extra insulation, airtightness and good windows, the running costs are reduced forever. Putting the extra effort in at the start means a better result that lasts. The “payback” if there must be one, is coming home every day from work and the house is warm, dry, fresh and healthy.
Bob climbed down from his ladder and explained how it was a little tricky at first taping around the windows and sealing to the floor with the INTELLO, but he soon got the hang of it.
“Putting the tapes around the windows takes a bit of time, but it wasn’t too bad.” Now that they’ve done it once, they are confident the next job will be a “piece of cake”.
He has seen a lot of changes in his lifetime, embracing change shows a growth mindset, an intention to move towards a better way. It shows wisdom.
The Blower Door test returned a result of 0.69 ACH, which is an excellent result! Anything less that 3 ACH is good, below 1 is great.
The whole build shows an attention to detail that only comes with experience and dedication.
“I’m looking to develop some units to the same standard”, says Bob.
The days of wooden tents are thankfully gone. This house has 140mm framing with Knauf insulation and the INTELLO vapour control layer installed.
“The industry is terribly slow on the uptake of Passive House. In early 2000 in Ireland there was nothing — now it is common practice."
“Group builders are building as cheap as they can which is good for the purchase price but what about the long-term running costs?” Bob wonders.
“In another 63 years Bob, what will we be living in? Ah, who knows — probably something completely different. The one constant is change”, he claims.