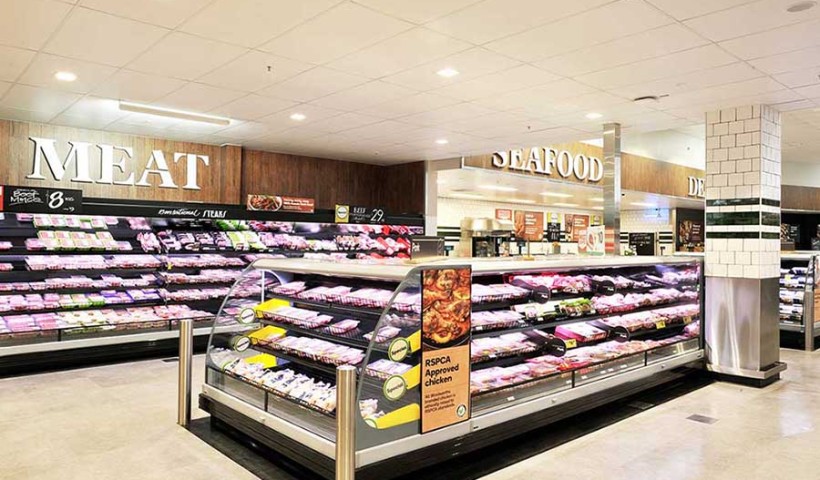
In the past, building consents were issued with a basic fire engineering report with little if any reference to specific fire stopping systems. Architects did not specify any fire stopping product or systems prior to consent and consequently, there was very little for the QS to base budgets on.
Traditionally each trade tried their hand at doing their own fire stopping or sub-contracting this out to specialist passive fire installers — at considerable cost. Compliance was the next hurdle and the cost of re-works and rectifications of non-compliant installations resulted in huge budget blow-outs.
When it is left to passive fire stopping installers to specify the penetration seal, their favourite option is the most labour-intensive option. Typically, the installers will not coordinate with other contractors or the project managers, resulting in the substrate not being prepared appropriately or the timing of the installations not being sequenced effectively.
With the introduction of new technology in fire mastics, the high-pressure expanding mastic (HPE) has paved the way for a multiple service — single point of entry — transit box to be developed.
BOSS Fyrebox
Tested to AS1530.4 (2014) the BOSS FyreBox can provide up to FRR -/120/120 and is capable of protecting the full range of apartment services through a single penetration. When installed in accordance with the manufacturer’s specifications it is compliant and cost-effective on a supply and install basis.
The specialist fire installation contractor is often not consulted in this process and the preparation of the building element (and the timing of this activity) leads to un-budgeted costs.
A simple feasibility exercise comparing the supply and install cost of a list of traditional fire stopping for individual services per apartment versus the cost of supply and install of a Boss FyreBox (including the cost of concrete drilling through slab walls) would illustrate the savings.
The BOSS FyreBox is a solution that has the construction industry challenging traditional installation methodology, in pursuit of the substantial cost reductions in the supply and install of tested (AS1530.4 – 2014) NZBC compliant fire penetration systems.
Specification is the answer
When an architect specifies the use of a cost-effective, compliant fire protection product/solution, the consent locks in the specification and control of the cost is awarded to the QS.
Inclusion of subject matter specialists at the design phase is the answer. The trick is in the timing of the involvement of Potters Passive Fire. The earlier we are engaged in the concept design phase the more effective our contribution would be in the overall cost saving on fire protection.
Where to find the true cost of passive fire
It is obvious that fire protection should not be left out of the design phase of the project. Project managers are concerned with getting the job done right the first time and on time. The quantity surveyor wants to get the project over the line within budget. The fire stopping installer wants to get the job done with the most labour-intensive solution possible.
Herein lie the conflict — cost of re-works and rectifications of non-compliant installations will be determined when the building consent authorities do their inspections. By then it is too late to do anything about budget blow-outs.
By involving the supplier early in the project design phase, the true cost of fire stopping can be more accurately determined, so all we need to do is talk to each other.