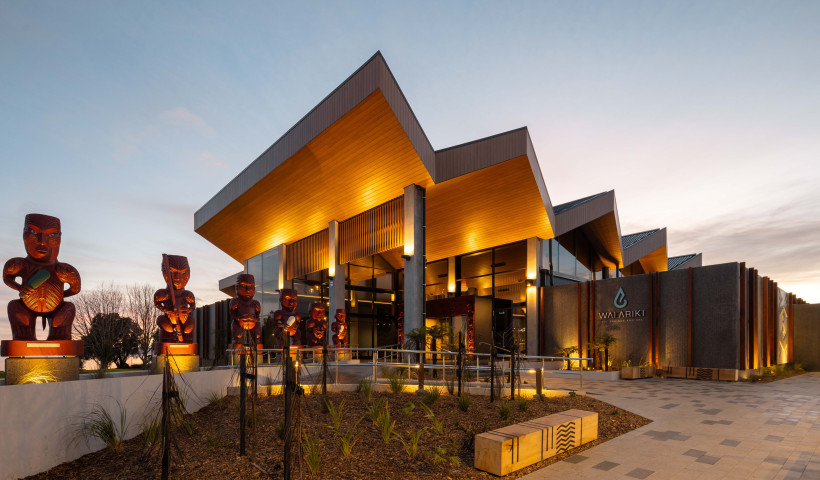
You are using an outdated browser version not supported by this website.
Click here to upgrade your browser
5,272 products with technical literature, drawings and more from leading suppliers of NZ architectural materials.
Case studies, new products and product news from leading suppliers of NZ architectural materials.
Blogs for architectural specifiers, offering product, design and business advice.
A new addition to Dimond’s existing mobile rollforming capability, the Roll to Roof service sees the mobile equipment craned to the building's roof level to rollform direct to the building, rather than the roof being rollformed at ground level then craned onto the roof for installation. This has multiple advantages, including removing the requirement for onsite material storage and reducing the site space required for processing.
Visit rolltoroof.co.nz for more information.
The Roll to Roof system streamlines the two-step process of rolling and shaping the steel roof at ground level and craning it into place, into one continuous process that is completed on the roof.
Two containers are used, the smaller one to hold the de-coiler, and a larger one to hold the roll forming machine. These containers are craned into place and are secured to anchor points during operation, with the containers being movable to different sections of the roof. The containers are also brought back to ground level for a coil change.
The pioneer project conducted using the Roll to Roof method was in conjunction with Kiwi Roofing Ltd on a 75,000m2 ;new distribution centre for Foodstuffs located within AIAL's The Landing Business Park. The project proved to be a real success, with demonstrated benefits including:
Two containers are used, the smaller one to hold the de-coiler, and a larger one to hold the roll forming machine. These containers are craned into place and are secured to anchor points during operation, with the containers being movable to different sections of the roof. The containers are also brought back to ground level for a coil change.
Test information available from Pacific Coilcoaters and BHP NZ Steel, and past history of use of long run metal roofing and cladding products in New Zealand indicate that, provided the product use and maintenance is in line with the guidelines contained in the current literature referenced, Dimond long run metal roofing & wall cladding systems can be expected to meet the performance criteria in clause B2 and E2 of the New Zealand Building Code, for a period of not less than 15 years.
Dimond is New Zealand's largest manufacturer of steel roofing, cladding, structural and rainwater goods.
Green Tag:
Dimond Roofing are a manufacturer of steel roofing, cladding and rainwater products.
Product EnquiriesNew and updated architectural products, design solutions, inspiration, technical advice and more when you sign up for EBOSS.