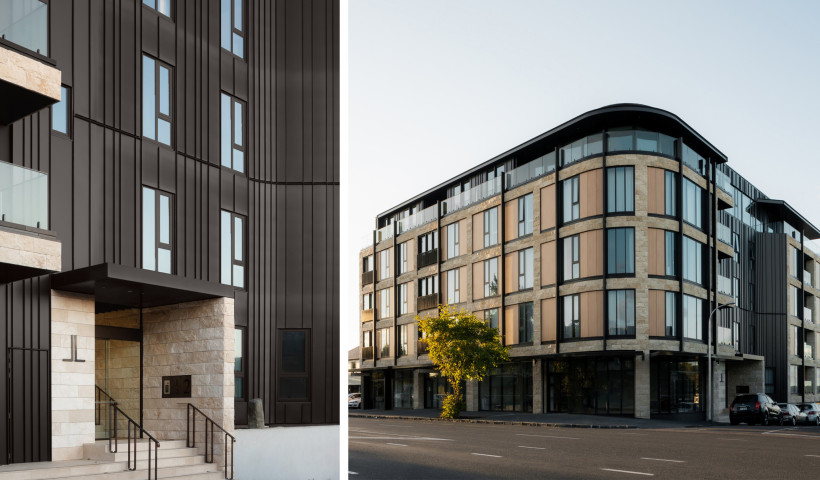
Its teams have quickly embraced the enormity and complexities of the task ahead. The company's initial concerns about working on a 45° or 38°roof pitch have proved accurate, and extreme care has been taken while working on these tricky surfaces. The uncompromised use of full harness and fall-restraint equipment is the order of the day.
'Luckily for us the weather has behaved itself, and besides a bit of rain the wind has stayed away. In saying that, shooting chalk lines in the rain doesn't really work for us,' says project manager Greg Hurt.
Each one of the 720 Smarttray standing-seam sheets on the roof have to be individually measured and hand-folded to incorporate the unique taper angle created by the conical shape of the roof.
'Initially we planned to work off CAD drawings but unavoidable minor variations in the as-built ply surface has forced the boys to resort to tried and tested measuring tools - the tape measure, string line and notepad!' says Architectural Metalformers factory manager Anthony Bell. 'From there we have had to devise a fast and efficient system to tranfer the site measurements back to our factory for production into Smarttray sheets. Just like a jigsaw puzzle, each completed sheet then gets a unique sequenced number that relates back to a specific place on the roof. It took a few days to perfect this process but now we have the engine fine tuned.'
The next phase is the real testing part of the roof: the kidney-bean-shaped north elevation, with its S-curved 70° roof pitch.
Follow the company's progress via the updated video blog.