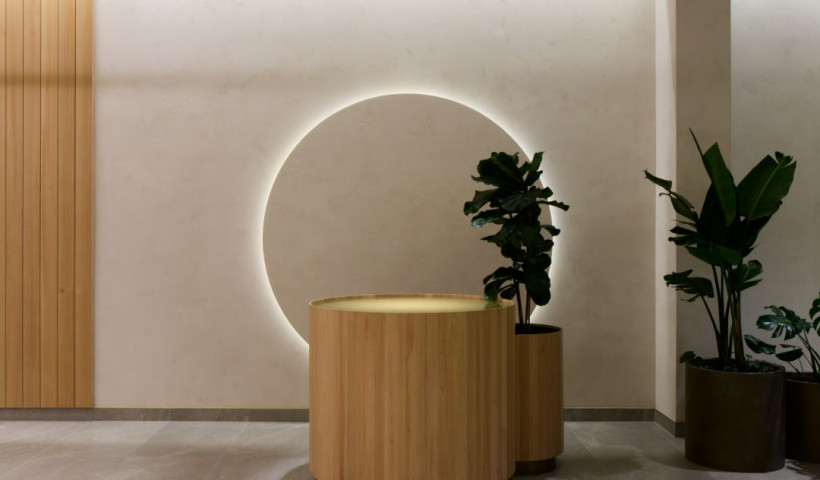
Aside from the obvious — safety — the number one concern of many residents in multi-residential developments around New Zealand is noise transfer between dwellings. Those living in apartment or intertenancy housing require good quality sound-resistance flooring and walls between dwellings.
Tiles and acoustics
Multi-level buildings with different tenancies are required under the NZ Building Code G6.2 and G6.3.2 to have acoustic properties of not less than llC 55. The standard states “The Impact Insulation Class of floors shall be no less than 55” or 50, which is the field test requirement (ie. not a laboratory test).
The Code requirement is not, however, the scale that acoustic engineers use to measure sound reduction which is Decibels (db) L n T,w. This scale has the same pass rate of 55, but is a reverse scale so the lower the decibel noise transfer the better.
Acoustic noise reduction systems, therefore, look to reduce or improve an existing floor to 55 Decibels (db) L n T,w or less in a total flooring systems test.
Below are examples of acoustic reduction systems on a bare concrete floor (without any additional reduction in decibels from other building elements like insulation and roof lining). This example is based on a concrete floor at an estimated worst-case 69 decibels which shows, that to achieve a pass rate, the last two systems are required. However, if the bare concrete system is closer to 59 decibels, all systems will take the floor into a pass position of 55 decibels or less.
Concrete floors
Tile Warehouse offers three systems to easily improve tiled concrete floors so that tile and stone pass the minimum requirement as part of the installation system. These incorporate acoustic elements that will significantly improve the floor’s quietness and will exceed code requirements over structural concrete substrates. In addition, tiled floors generate superior lifecycle costings, thermal mass calculations, and basically ease of living.
Acoustibond and Acoustiflor systems are:
- Green friendly and made from recycled rubber crumb (Green Star compliant)
- Part of a comprehensive warranted tiling system
- Trowel applied
- Cost-effective
- Made and backed by a highly reputable company
- Designed to eliminate the bounce back reverberation common with loose laid flooring systems, i.e. no 'drummy' sounds in the room.
Most bare concrete floors have an IIC of between 59 and 69. These variations are due to design and construction techniques, so we have different systems to cope with these variations.
As a guide, a 3dB reduction is clearly noticeable, and a 10dB reduction is half as loud.
Tile Warehouse's systems:
System 1: Acoustibond, a flexible 2-pack adhesive
- Trowel-applied, using a 12mm notched trowel. Tiles over 450 x 450mm are also back-buttered
- Gives an improvement Delta ΔLw (i.e. noise reduction of...) of 10dB, so will pass the Code requirements over most concrete floors (subject to on-site test of existing floor)
- The tiler simply tiles
- No added layers
- No added height
- Minimal added cost
System 2: Acoustiflor, a flexible, self-levelling compound
- Gives an improvement Delta ΔLw (i.e. Noise reduction of...) of 12dB once tiled with Monoflex
- Can be installed at any stage after the base plates are in
- Can be installed internally and externally
- When tiled with Monoflex, will pass the code over most structural concrete floors
- Covers minor level change, usually eliminating the need for FLCs
- Can encapsulate underfloor heating, eliminating the need for an extra layer
- Is only 6mm thick, plus adhesive
- Can be installed at 200m²+ per day
- Acts as a permanent crack suppression system.
System 3: Acoustiflor Plus, a flexible, self-levelling compound
- Gives an improvement Delta ΔLw (i.e. Noise reduction of...) of 14dB once tiled with Acoustibond
- Can be installed at any stage after the base plates are in
- Can be installed internally and externally
- When tiled with Acoustibond, will pass the Code over any structural concrete floor
- Covers minor level change, usually eliminating the need for FLCs
- Can encapsulate underfloor heating, eliminating the need for an extra layer.
To meet the Code:
To ensure you conform to the 'Airborne and Impact Code', firstly you need to design a suitable floor substrate as this will dictate the acoustic system/adhesive system required.
For superior substrates:
- 200mm concrete slab
- 300mm suspended ceiling
- 10mm plasterboard
Use System 1: Tile with Acoustibond to conform to code (there is a minimal cost estimate of $10/m²)
For average substrates:
- 170mm concrete slab
- 100mm suspended ceiling
- 10mm plasterboard
Use System 2: Tile with Monoflex over Acoustiflor (check with Acoustic Consultant as to the specific rating of the structure. Acoustiflor at 3, 4.5 or 6mm thick may be required; approximate cost $30 - $50 /m²)
For less than desirable substrates (more design required)
- 150mm concrete slab
- 50mm suspended ceiling
- 10mm plasterboard
Redesign or use System 3: Tile with Acoustibond over Acoustiflor at 6mm thick (there is the cost to counteract the substrate of approximately $65/m²).
Wet areas
The results above are further improved by installation in wet areas, as the addition of Liquid Flash 2-pack or Hydrathane waterproofing membranes in the system increases performance.