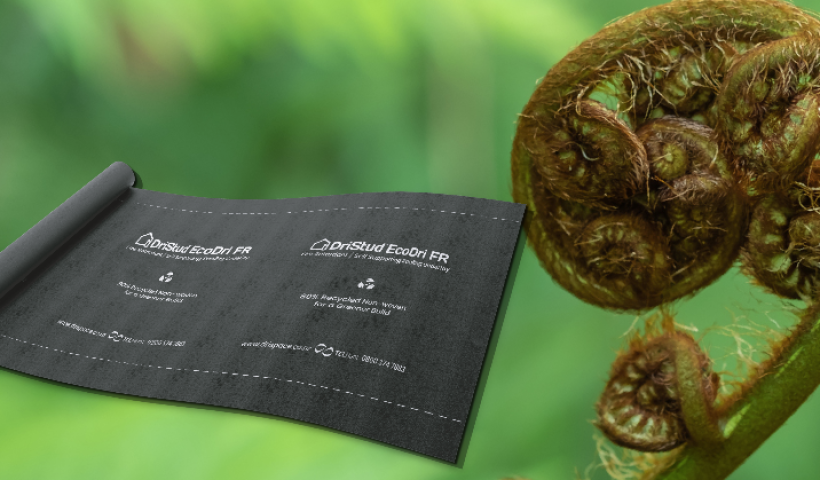
The team at DriStud often hears about how much condensation there is in winter. Normal condensation is easily understood. Condensation occurring on a cold surface like windows can be easily cleaned away.
Then there are areas where it is difficult to access, such as the roof. The condensation forms under the iron, hence why underlay is installed to absorb or collect the moisture until it evaporates when the temperatures rise during the daytime.
What is of concern is interstitial (meaning forming or occupying) condensation as it cannot be seen. It occurs when moisture is generated internally around the house or building. The warm moist air penetrates inside a wall floor or upwards into the ceiling cavities. It reaches its ‘dew point’ and it turns into liquid and pools, soaking into and rotting timbers and other materials. As it is not visible and not cleaned away, over time the condensation simply lingers which can result in mould as well as long-term structural damage.
The main sources of interstitial condensation are listed below:
- Bathing, showering, cooking, gas heating
- Clothes drying, respiration, perspiration
- Wet construction materials
- Concrete floors — during curing, a 100mm thick concrete slab releases approximately 10L of water vapour per m² of surface area
The moisture generated from above needs to be vented and the best way to do it is by opening windows. The problem is it is not always possible. The air movement needs to be sufficient to keep the humidity to a level that the synthetic underlay under the metal roof cladding can work within its intended capacity.
Supposed and perceived problems with synthetic underlays have not been found to be with the product, but with the overload of attic moisture due to lack of ventilation of moisture from below. Most condensation forms on the underside of the underlay, because while roofing underlays are permeable they still form a substantial vapour check, and as they are in contact with the roof, they are at a similar temperature.
As a synthetic roof underlay supplier, DriStud focuses on engineering products to suit NZ weather conditions. To help minimise roof cavity condensation, they have used non-woven fibres to improve moisture absorbency and holding capacity. Now all DriStud underlays hold 240gsm of moisture where the requirement is 150gsm. The products pass retention of condensate tests which were carried out by BRANZ.
To minimise roof cavity condensation, it is recommended to follow recommendations from the NZ Metal Roofing Manufacturers (MRM) Code of Practice v3.0.
Recommendations:
- Use sufficient ventilation to minimise condensation.
- Kitchen, bathroom and clothes dryer fans should be vented outside, not into the attic spaces.
- Do not push insulation up hard against the underside of the roofing material; a minimum air gap of 25mm is required
- Avoid direct fixing where condensation risks are high. Have an air gap between the metal cladding and synthetic underlays.
- Underlay should terminate at the ridge purlin, or have strips or slots cut in it where it traverses the apex.
- Do not use non-perforated profiled filler strips at the eaves and apex.
- Skillion and flat roofs and any other high-risk designs (curved roofs) must be ventilated to comply with the NZMRM Code of Practice.
- Educate occupants: avoid unvented gas heating and kerosene heaters. Try to minimise sources of moisture and open a window when possible.