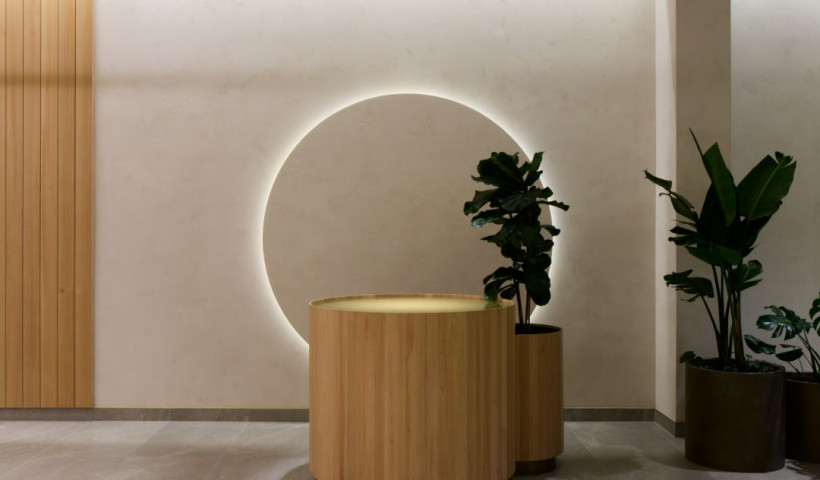
Aside from the obvious — safety — the number one concern of many residents in multi-residential developments around New Zealand is noise transfer between dwellings. Those living in apartment or intertenancy housing require good quality sound-resistance flooring and walls between dwellings.
Tiles and acoustics
Multilevel buildings with different tenancies are required under the NZ Building Code G6.2 and G6.3.2 to have acoustic properties of not less than llC 55. The Standard states “The Impact Insulation Class of floors shall be no less than 55” or 50, which is the field test requirement (ie not a laboratory test).
The Code requirement is not, however, the scale that acoustic engineers use to measure sound reduction which is Decibels (db) L n T,w. This Scale has the same pass rate of 55, but is a reverse scale so the lower the decibel noise transfer the better.
Acoustic noise reduction systems, therefore, look to reduce or improve an existing floor to 55 Decibels (db) L n T,w or less in a total flooring systems test.
Below are examples of acoustic reduction systems on a bare concrete floor (without any additional reduction in decibels from other building elements like insulation and roof lining). This example is based on a bare concrete floor at an estimated worst-case 69 decibels which shows, that to achieve a pass rate, the last two systems are required. However, if the bare concrete system is closer to 59 decibels, all systems will take the floor into a pass position of 55 decibels or less.
Concrete Floors
Tile Warehouse offers three systems to easily improve tiled concrete floors so that tile and stone pass the minimum requirement as part of the installation system. These incorporate acoustic elements that will significantly improve the floor’s quietness and will exceed code requirements over structural concrete substrates. In addition, tiled floors generate superior lifecycle costings, thermal mass calculations, and basically ease of living.
Tile Warehouse's Acoustibond and Acoustiflor systems are environmentally-friendly and made from Recycled Rubber crumb (Green Star Compliant), part of a comprehensive warranted tiling system, trowel applied, cost-effective, and made and backed by a highly reputable company. The systems are designed to eliminate the “bounce back” reverberation common with loose laid flooring systems, i.e. no 'drummy' sounds in the room.
Most bare concrete floors have an llC of between 59 and 69. These variations are due to design and construction techniques, so Tile Warehouse offers different systems to cope with these variations. Your acoustic engineer can give you more details on your floors.
As a guide, a 3dB reduction is clearly noticeable, and a 10dB reduction is half as loud.
Tile Warehouse's systems:
System 1: Acoustibond, a flexible 2-pack adhesive
- Trowel-applied, using a 12mm notched trowel. Tiles over 450 x 450mm are also back-buttered
- Gives an improvement Delta ΔLw (I.e. Noise reduction of...) of 10dB, so will pass the Code requirements over most concrete floors (subject to on-site test of existing floor)
- The tiler simply tiles
- No added layers
- No added height
- Minimal added cost
System 2: Acoustiflor, a flexible, self-levelling compound
- Gives an improvement Delta ΔLw (I.e. Noise reduction of...) of 12dB once tiled with Monoflex
- Can be installed at any stage after the base plates are in
- Can be installed internally and externally
- When tiled with Monoflex, will pass the code over most structural concrete floors
- Covers minor level change, usually eliminating the need for FLC’s
- Can encapsulate underfloor heating, eliminating the need for an extra layer
- Is only 6mm thick, plus adhesive
- Can be installed at 200m²+ per day
- Acts as a permanent crack suppression system
System 3: Acoustiflor Plus, a flexible, self-leveling compound
- Gives an improvement Delta ΔLw (I.e. Noise reduction of...) of 14dB once tiled with Acoustibond
- Can be installed at any stage after the base plates are in
- Can be installed internally and externally
- When tiled with Acoustibond, will pass the Code over any structural concrete floor
- Covers minor level change, usually eliminating the need for FLC’s
- Can encapsulate underfloor heating, eliminating the need for an extra layer
To meet the Code:
To ensure you conform to the “Airborne and Impact Code”, firstly you need to design a suitable floor substrate as this will dictate the acoustic system/adhesive system required.
1. Superior Substrate
- 200mm concrete slab
- 300mm suspended ceiling
- 10mm plasterboard
Use System 1: Tile with Acoustibond to conform to code (there is a minimal cost estimate of $10/m²)
2. Average Substrate
- 170mm concrete slab
- 100mm suspended ceiling
- 10mm plasterboard
Use System 2: Tile with Monoflex over Acoustiflor (check with Acoustic Consultant as to the specific rating of the structure. Acoustiflor at 3, 4.5 or 6mm thick may be required; approximate cost $30 - $50 /m²)
3. Less than desirable substrate (more design required)
- 150mm concrete slab
- 50mm suspended ceiling
- 10mm plasterboard
Redesign or use System 3: Tile with Acoustibond over Acoustiflor at 6mm thick (there is the cost to counteract the substrate of approximately $65/m²).
Wet areas
The results above are further improved by installation in wet areas, as the addition of Liquid Flash 2-pack or Hydrathane waterproofing membranes in the system increases performance.
E3/AS1 Build Code Change
If you are a specifier in New Zealand, you will by now be aware of the Building Code Change which came into effect Nov 2021 regarding internal moisture and flooring. The code has been put into place to protect tenants of apartments and multi-residential dwellings.
Tile or full-sheet vinyl are the only flooring options immediately accepted by councils in areas that are within 1.5 metres of sanitary fixtures or sanitary appliances. This description not only encompasses bathrooms, toilets and laundries but now also kitchens and some adjoining areas within 1.5 metres of fixtures and appliances.
Now with only two acceptable solutions, it is clear there is more focus on ensuring there is containment of water and protection of surrounding areas and adjoining tenancies.
Safety and fire performance
Ceramic tiles, being fire-resistant, are an obvious choice for both floor and wall surfaces for intertenancy, multi-residential dwellings.
Ceramic and porcelain tiles are non-combustible so do not catch fire nor do they give off toxic fumes, affecting breathing, when exposed to fire.
In New Zealand, fire ratings are required by the Building Code to ensure that if a building is on fire, its construction materials do not significantly increase the spread or intensity of a fire.
However, fire safety requirements do not necessarily apply for tiles, considering that ceramics are a fire-resistant material, most being manufactured at over 1000°C. For example, if a lit cigarette is dropped on the floor, in most circumstances it will not do any damage to the tile. Even hot kitchen pans or skillets will not scorch or melt the surface of tile, let alone catch on fire.
During a fire, many household products let off dangerous toxic fumes in the form of VOCs (volatile organic compounds). However, being fired at very high temperatures means ceramic tiles do not exude VOC emissions. During manufacture, any organics that might be present in clays or binders are completely burned away. As a result, the final product is inert and no VOCs can be emitted. Aside from this, quality porcelain tiles contain no sealants, waxes or other chemicals that could release VOCs into the environment.
A safe and simple approach with regards to fire performance in products is to utilise tile for both floor and wall areas.
With over 100 years of tile experience, Tile Warehouse's Commercial Representatives are available to assist you with specification and best fit-for-purpose products for your upcoming projects.